Enabling Automated Quality Control in Composites for Less Scrap, Higher Yield
As industries advance new bio-based, faster reacting and increased recycled content materials and faster processes, how can manufacturers quickly establish and maintain quality control?
On-Demand Webinar
Manufacturers often struggle with production anomalies that can be traced back to material deviations. These can cause fluctuations in material flow, cooling, and cure according to environmental influences and/or batch-to-batch variations. Today’s competitive environment demands cost-efficient, error-free production using automated production and stable processes. As industries advance new bio-based, faster reacting and increased recycled content materials and faster processes, how can manufacturers quickly establish and maintain quality control?
In-mold dielectric sensors paired with data analytics technology enable manufacturers to:
- Determine glass transition temperature in real time
- Monitor material deviations such as resin mix ratio, aging, and batch-to-batch variations throughout the process
- Predict the influence of deviations or material defects during the process
- See the progression of curing and demold the part when the desired degree of cure, Tg or crystallinity is achieved
- Document resin mix ratios using snap-cure resins for qualification and certification of RTM parts
Successful case histories with real parts illustrate how sensXPERT sensors, machine learning, and material models monitor, predict, and optimize production to compensate for deviations. This Digital Mold technology has enabled manufacturers to reduce scrap by up to 50% and generated energy savings of up to 23%.
On-Demand Webinar
- Dealing with the challenge of material deviations and production anomalies
- How dielectric sensors work with different composite resins, fibers and processes
- What is required for installation
- Case histories of in-mold dielectric sensors and data analytics used to monitor resin mixing ratios and predict potential material deviations
- How this Digital Mold technology has enabled manufacturers to optimize production, and improve quality and reliability
Our speaker
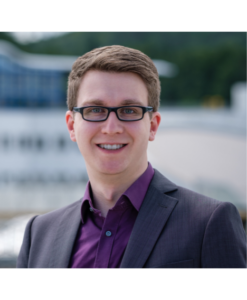
Dr. Nicholas Ecke
sensXPERT Application Engineer
nicholas.ecke@sensxpert.com
Since October 2022, Dr. Nicholas Ecke has joined the NETZSCH Process Intelligence GmbH team around Dr. Alexander Chaloupka. The application engineer studied process and medical engineering at the Technical University of Munich and was a chief engineer at the Chair of Composite Materials at the Technical University of Kaiserslautern. In 2021, he completed his doctorate in engineering with his dissertation, which was awarded the Oechsler Prize. The thesis dealt with methods and approaches for developing and designing tribological components made of plastics. As a sensXPERT, Dr. Nicholas Ecke takes care of the smooth integration of the intelligent sensor technology sensXPERT Digital Mold in the production processes of customers worldwide.