Beyond Black Boxes: Overcoming In-Mold Material Deviations
Plastics manufacturing holds immense potential for innovation and advancement across countless industries.
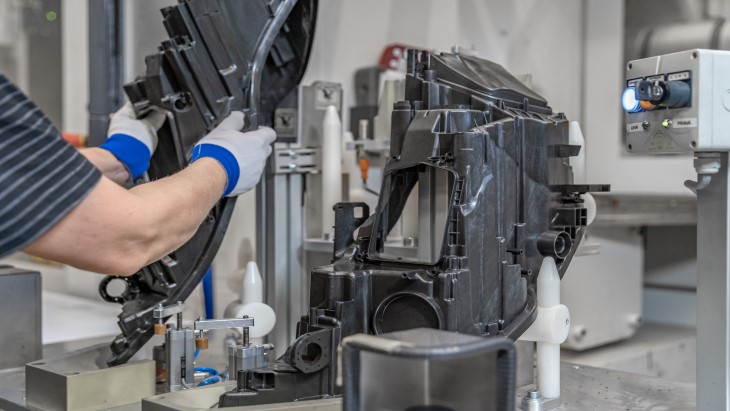
But what happens when the very heart of the production process, the in-mold material behavior, remains hidden behind a ‘black box’? Inconsistent quality, increased scrap rates, and higher energy consumption become costly obstacles, hindering efficiency and profitability.
While the desired outcome is a perfectly formed product, the reality often involves unpredictable material behavior leading to deviations like shrinkage, warpage, and voids. At the same time, closed-mold processes and limited data visibility make it difficult to pinpoint the root causes of these deviations.
In this article, we explore the consequences of ‘black box’ processes and analyze the challenges they pose for production efficiency and quality control. Further along, we present a solution to demystify material behavior within the manufacturing ‘black box’ and help manufacturers gain full control of their processes.
Material Behavior Deviations
Whether dealing with thermosets, thermoplastics, or elastomers, the closed-mold process promises precision but often faces unseen challenges that manifest as deviations in material behavior. These deviations can significantly impact the final product’s quality, functionality, and aesthetics.
- Dimensional Instability: Whether it is shrinkage, warpage, or distortion, deviations in final part dimensions can occur due to factors like uneven temperature, mold design, material properties, and processing parameters. This can lead to parts that do not meet specifications, impacting functionality, assembly, and overall quality.
- Internal Defects: Trapped air, gases, or contaminants can create voids, bubbles, or inclusions within the molded material. These internal defects weaken the structure, potentially affecting performance and compromising safety.
- Surface Imperfections: Flow lines, sink marks, and roughness on the finished surface can arise from issues like injection pressure, temperature control, or material properties. These imperfections not only damage the product’s aesthetics but can also impact its functionality.
- Inconsistent Properties: Variations in material properties throughout the molding process can lead to inconsistencies in strength, flexibility, or other desired characteristics. This can compromise product performance and reliability.
Understanding the source of these deviations is crucial for all closed-mold processes. However, the opaque nature of traditional methods often makes it difficult for plastics processors to determine the exact cause of error. This lack of transparency can hinder optimization efforts and leaves manufacturers struggling to control and predict material behavior within the mold.
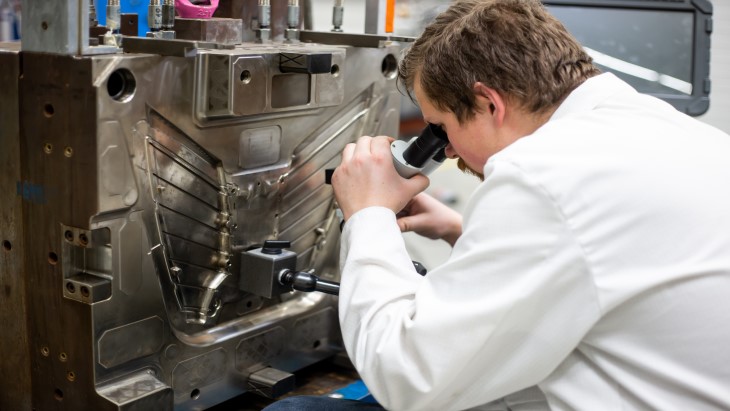
The Consequences of the Manufacturing ‘Black Box’
The manufacturing ‘black box’, due to which crucial details about material behavior remains difficult to visualize or understand, comes with significant consequences that impact plastics manufacturers on various levels.
For one, without continuous insight into in-mold material behavior, inconsistencies in the final product are more likely to occur. A manufacturing environment with fluctuating product quality can face potential safety hazards and, ultimately, customer dissatisfaction.
Additionally, unforeseen deviations often translate to unusable products, resulting in increased scrap rates and wasted materials. This in turn leads to financial losses that impact production efficiency and profitability.
Furthermore, troubleshooting errors in opaque processes is time-consuming and costly. The lack of data makes it difficult to uncover the source of deviations, leading to trial-and-error adjustments and extended downtime, which impedes production efficiency and increases operational costs.
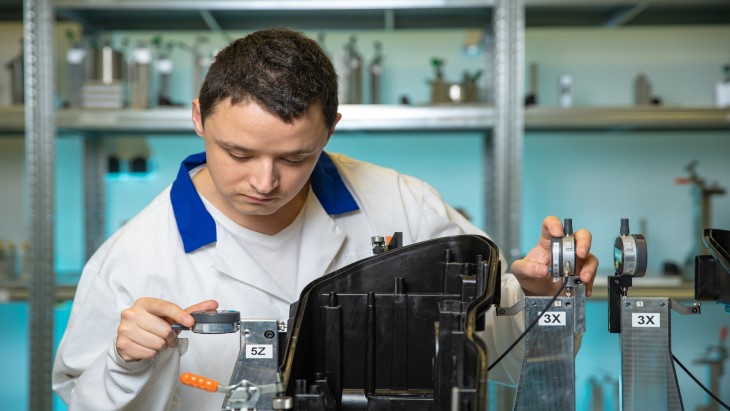
The consequences of the manufacturing ‘black box’ extend beyond immediate production concerns. They impact brand reputation, customer trust, and the ability to compete in a market that increasingly demands transparency and sustainability.
From Black Box to Controllable System
Historically, closed-mold manufacturing has been constrained by a lack of real-time insights into material behavior within the mold, hindering process optimization and quality control. This ‘black box’ phenomenon has resulted in inconsistencies, inefficiencies, and ultimately, limitations in achieving optimal production outcomes.
However, advancements in sensor technology, data analytics, and modeling tools are paving the way for a paradigm shift. sensXPERT Digital Mold stands as a solution that empowers manufacturers to transition from opacity to controllability and unlock the full potential of their closed-mold processes.
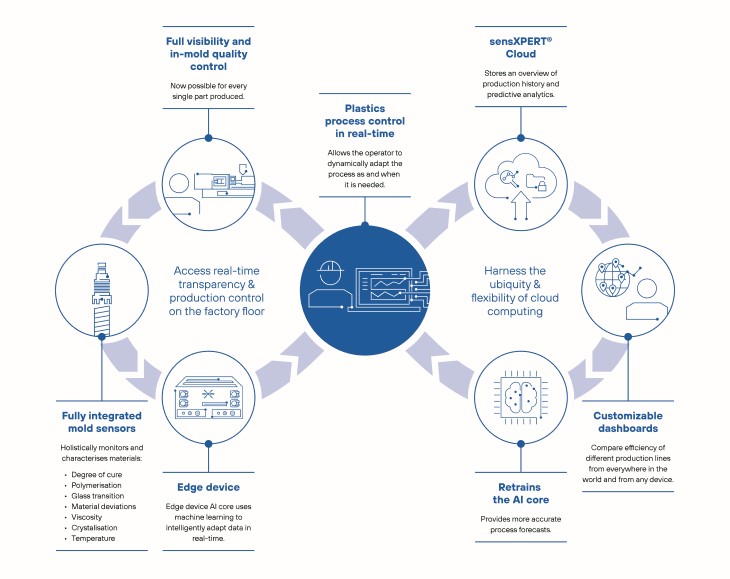
Integrated Sensor System for Comprehensive Data Acquisition
At the core of the sensXPERT Digital Mold Solution lies advanced sensor technology embedded directly within the mold cavity. These sensors capture many crucial parameters in real-time, including viscosity, degree of cure and crystallization, glass transition temperature, and more within the solidifying material.
This comprehensive data acquisition offers complete visibility into the previously opaque environment, enabling processors to locate potential deviations and proactively address them.
Advanced Analytics and Machine Learning for Predictive Optimization
sensXPERT Digital Mold goes beyond data collection. Advanced machine learning algorithms are hosted on the sensXPERT Edge Device to process the acquired sensor data and historical process records. These algorithms identify patterns, predict process outcomes, and, through the WebApp, visualize a process’ trajectory.
This predictive capability allows manufacturers to proactively adjust process parameters, such as temperature or pressure, to ensure consistent material behavior and product quality throughout production cycles.
Continuous Learning and Sustainable Performance Improvement
sensXPERT’s machine learning algorithms constantly evolve by analyzing vast datasets and incorporating insights from each process cycle. This ongoing retraining leads to progressively refined predictions and recommendations that enable manufacturers to achieve ever-improving process optimization and minimize material waste.
Additionally, the system’s focus on real-time monitoring and dynamic process adjustments contributes to a more sustainable manufacturing environment by reducing consumption and minimizing scrap generation.
sensXPERT’s comprehensive Digital Mold Solution empowers processors to go beyond the traditional limitations of ‘black box’ manufacturing and make use of their production’s full potential.
Would you like to learn more about overcoming material deviation challenges? Read our technical guide, ‘Conquering Material Deviations in Plastics Manufacturing’.
