How to Improve Quality Control in Elastomer Manufacturing
Elastomers are a class of polymers that have unique elastic properties. The term for this polymer stems from its ability to recover to its original form after extensive stretching; specifically stemming from ‘elastic polymer’. Elastomers are ideal for applications in which flexibility and resilience are necessary.
The key characteristics of elastomers include flexibility – they can undergo significant deformation without permanent damage – resilience – they can return to their original shape following deformation – and high elasticity – they can stretch to several times their original length.
Our society depends on elastomers. From sport and leisure activities to health care, transportation, and material handling, elastomers – or rubber – can be found in almost all of our everyday products. Due to their high resistance to heat, oil, acids, and mechanical stress, elastomer materials like NBR and EPDM are used to produce tires, sealing rings, tubing, and a wide variety of other products.
This article describes the properties of different elastomer materials, their applications, and elastomer manufacturing processes. We will also introduce one of our partners, their core business, and how sensXPERT collaborated with them to increase efficiency in their rubber stator production.
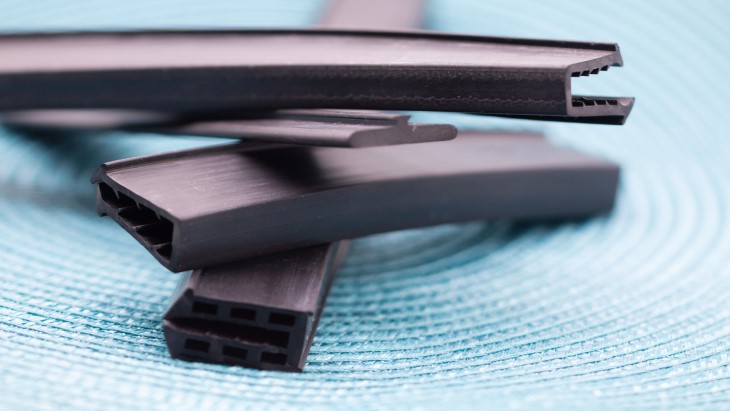
What are Elastomers?
Elastomers, recognized for their elasticity, have a unique molecular structure. This class of polymers is made up of long polymer chains that are formed from specific building blocks called monomers. The chains are created through a process called polymerization.
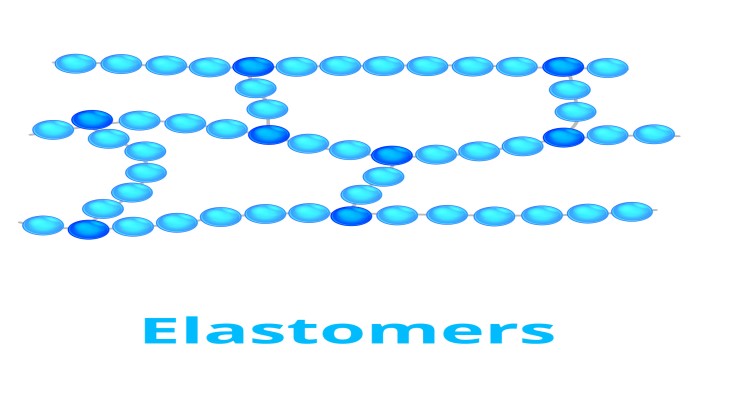
What sets elastomers apart is the addition of cross-linking agents, such as sulfur, during vulcanization – a process that originated in the 19th century. Developed by Charles Goodyear, vulcanization involves subjecting elastomers to heat and sulfur, creating strong connections between the polymer chains.
This breakthrough not only enhanced the strength and durability of elastomers, but also provided them with the ability to stretch and recover their original shape, revolutionizing their applications in various industries.
The presence of flexible bonds and the unique twisted arrangement of these polymer chains contribute to the remarkable elasticity and flexibility of elastomers, making them indispensable in countless products and manufacturing products today.
Types of Elastomer Materials
Elastomers encompass a diverse range of materials, each tailored to specific applications based on their distinct properties. The choice of elastomer depends on factors such as temperature resistance, chemical compatibility, and mechanical properties.
The following table illustrates the various types of “commercially important elastomers” (Britannica), their properties, and common applications:
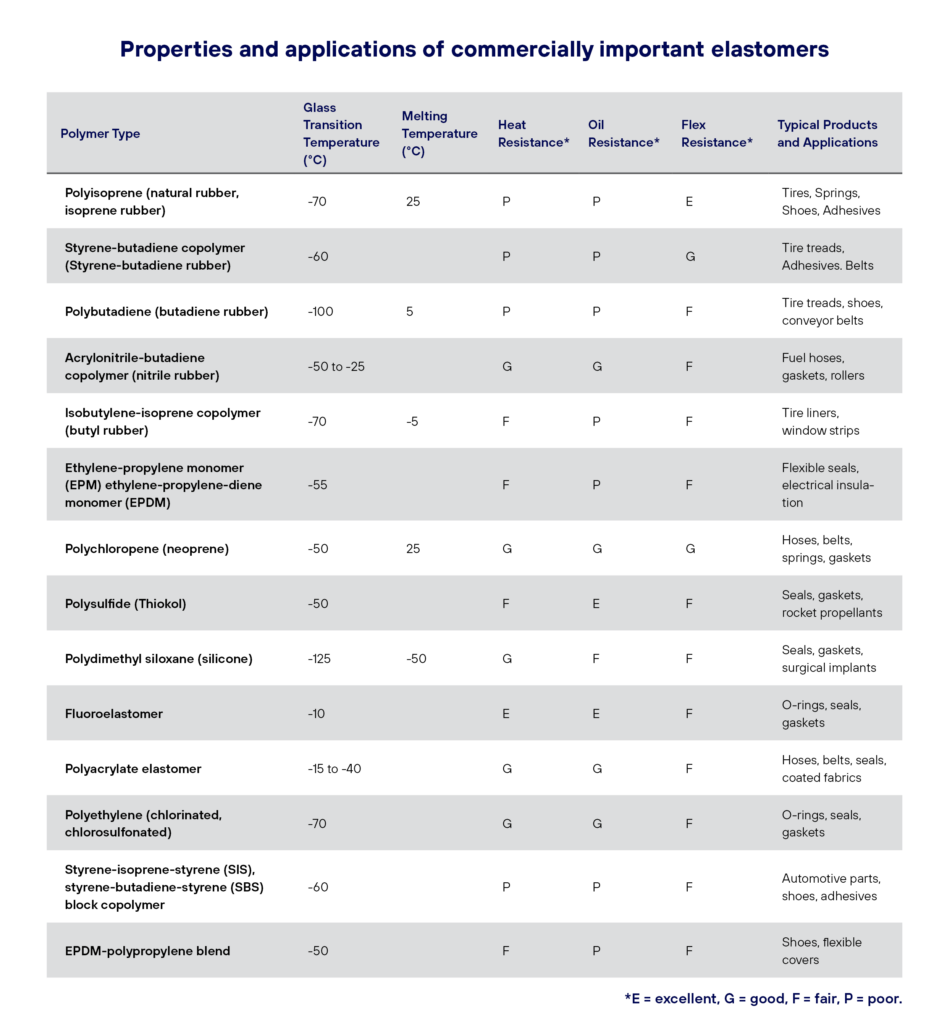
This wide array of elastomer materials highlights the versatility of these polymers in meeting diverse industrial needs. Understanding the specific properties and applications of each type is crucial for manufacturers to choose the most suitable elastomer for a given purpose. As technology advances, the development of new elastomer formulations continues, further expanding the possibilities for innovative applications.
Elastomer Manufacturing
Elastomer part production involves several manufacturing processes to shape, cure, and finish the elastomeric materials into the final products. Some common manufacturing processes used for elastomer parts include:
- Extrusion: elastomeric material is pushed through a die to create continuous profiles, such as tubes, hoses, or seals.
- Injection Molding: molten elastomer materials is injected into a mold cavity, where it solidifies to form the desired shape.
- Compression Molding: elastomeric materials is placed in an open mold, and the mold is closed under pressure to shape and cure the material.
- Transfer Molding: similar to compression molding, but the elastomer material is preheated before being transferred into the mold cavity under pressure.
- Rotational Molding: powdered elastomer is placed in a mold, which is roatated in an oven. The material melts and coats the interior of the mold.
Each of these manufacturing processes offers distinct advantages depending on the desired part geometry, volume, and material properties. Quality control measures are crucial at each stage to ensure the consistency and reliability of elastomer parts in various applications.
Introducing our Partner and Their Core Business
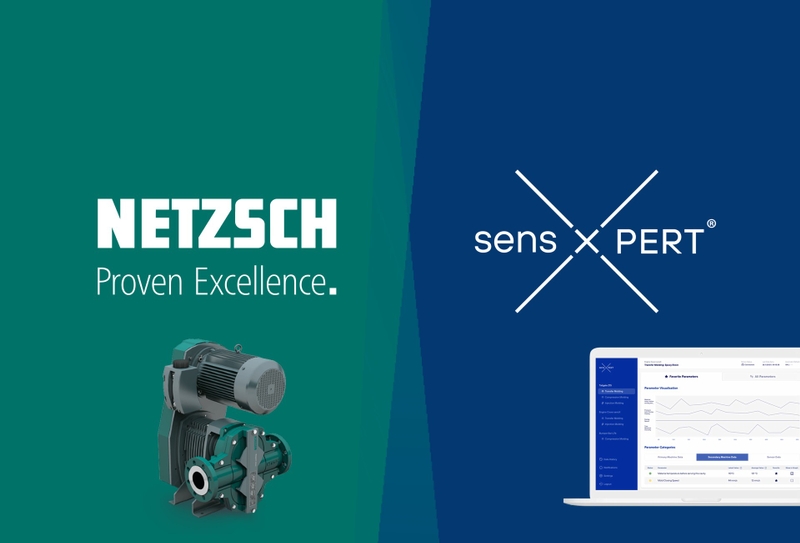
Our affiliated company, NETZSCH Pumps & Systems, is the leading supplier of positive displacement pumps and boasts more than six decades of experience in the field. Designed specifically for difficult pumping situations, NETZSCH pumps range in size from the industry’s smallest metering pumps to high volume pumps for applications in the oil and gas or mining industries.
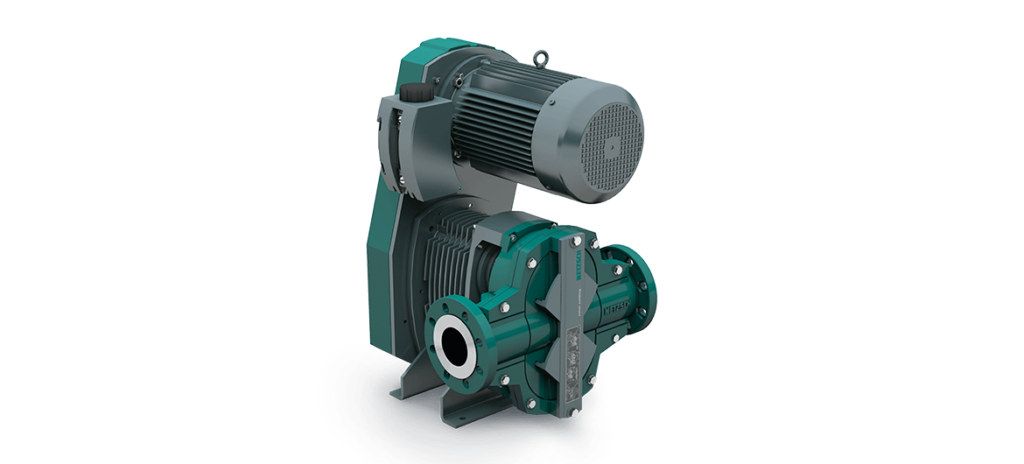
Alongside the supply of state-of-the-art pump solutions, the company’s core expertise is in-house research & development as well as elastomer manufacturing. The raw material is used in stators, rotary lobes and housing inserts. NETZSCH also develops and manufactures rotors in various geometries, made of various metallic and ceramic materials for optimum performance and service life.
The Challenge: Insufficient Information About Material Properties During Processing
During the production of rubber parts, the raw material is heated and remains in the heated mold until the molecules sufficiently crosslink and form an irreversible bond. This crosslinking reaction or vulcanization is responsible for the final properties and thus quality of the product. Insufficient crosslinking leads to low-quality parts. It is characteristic for all elastomers to show a weak crosslinking reaction. Paired with a high filler content of carbon black, material characterization using a common thermal analysis technique is tricky and does not produce sufficient results to fully understand common material deviations in different batches, which is important to adapt the production process and reduce scrap.
This is the challenge NETZSCH Pumps & Systems faces. Currently, the company controls the quality of the incoming raw material and has pre-defined process parameters for all types of used raw materials. For the incoming material control, the company uses a rheometer and measures mechanical properties of the incoming elastomers.
While this approach is common practice in many polymer industries, variations in the process and the processed material are still not fully understood. As a result, parts of low quality are only detected in a downstream post-process quality control step.
The Solution: Data-Driven, Real-Time Process Optimization
sensXPERT supplied its solution to optimize the production process of elastomer parts using real-time data from the material, machine, and process. A special sensor designed for polymers with electrically conductive and water-containing components is used for monitoring elastomer vulcanization in real-time.
Measuring the crucial material properties during the production process of elastomer parts allows for data-driven process optimization. This way, quality control moves into the production process and immediate qualitative results are generated from the effective use of production data. All data is visualized in a customizable dashboard, giving an overview of all production processes equipped with sensXPERT.
sensXPERT is the first solution that allows real-time monitoring of rubber vulcanization during the production process. NETZSCH Pumps & Systems was the first industrial partner to use this technology before sensXPERT’s commercial launch in 2022.

“During the curing time, the machine is closed and no one knows what happens inside on a molecular level. Thus, the process is like a black box. Typically, a fixed heating time is set for a part to get the demanded degree of cure, which should give the part its optimal mechanical properties. However, there are different influences on the material, like variety in batches, mold temperatures and environment. To cope with these influences, the heating time is preventively extended. This is the so- called fear factor.
With help from sensXPERT®, we can now see what happens inside the material when the mold is closed. The solution measures the degree of cure, predicts the process through the collected data and stops heating at the exact point, when the optimal mechanical properties are reached. Thus, sensXPERT® empowers us to produce complex parts at highest quality and save machine time leading to lower production costs and higher output. That’s why we are very excited to be a one of the first partners in this area.”
Frank Götz, Process Engineer at NETZSCH Pumps & Systems
“We expect the new technology to increase efficiency by significantly reducing cycle times. We are very pleased to be able to support our corporate venture sensXPERT® through this collaboration and to generate added value for ourselves. This AI-based technology perfectly supports our aspiration to further automate and digitize our value chain.”
Jens Heidkötter, Managing Director at NETZSCH Pumps & Systems
Initial results of the sensXPERT and NETZSCH Pumps & Systems collaboration demonstrate the potential for a 15% cycle time reduction in their production of rubber stator parts.
Want to read more about the collaboration? Read our success story here: NETZSCH Pumps & Systems Success Story