The Impact of Composites in the Aviation Industry
The aviation industry is ripe-full of advancements and transformation. Materials and processes have evolved ever since the development of the first powered flight by the Wright Brothers in 1915, which was built out of wires, canvas, wood, and steel. The 1920s and 1930s saw a material transition to metals such as aluminum. This was seen as a metamorphosis into lightweight and durable aircraft manufacturing.
The post-war period saw even more material advancements with the introduction of titanium, a material that is resistant to fatigue, corrosion, and high temperatures. However, titanium quickly proved to be very costly and limited in availability.
First used in the 1940s, “[g]lass fibre-reinforced plastic [GFRP], or fiberglass, was the first lightweight composites material to be found in aircraft” (Airbus). An evolution towards the use of carbon fibre marked the material landscape of the 1970s to 1980s, and, in our present day, carbon fibre-reinforced composites (CFRP) have become standard in aviation manufacturing, especially due to their lightweight properties.
Aviation manufacturing processes also have a rich history of technological advancement. During World War I, a time of wood and canvas material usage, skilled woodworkers and experienced sewers created parts – such as wooden frames and skins for wings and fuselages – by hand.
When metal became the material of choice, processes adapted accordingly. This included the manual cutting, shaping, bending, and forming of metals, as well as employing processes like welding and flush riveting.
With the rise of composites, the traditional metalworking machinery became overcast by other machinery, for example the autoclave, which will be further elaborated upon in next week’s blog article. In this article we are exploring why plastics and composites are used in aviation manufacturing, what advantages they bring, and recent material innovations that are enhancing the use of plastics in aviation applications.

The Advantages of Plastics and Composites in Aviation Manufacturing
It is collective understanding that aircraft undergo extreme temperatures, pressures, and stress. Accordingly, the utilization of plastics and composite materials has been propelled by their capability to endure such high-performance applications.
There are many motivations behind using plastics and composite materials in manufacturing aviation structures. These considerations include weight reduction, durability, design factors, less required maintenance, noise reduction, improved fuel efficiency, and corrosion resistance.
Weight Reduction and Improved Fuel Efficiency: Being one of the most critical factors in aviation, plastics and composites contribute to weight reduction and are lighter than traditional materials like metal. By reducing an aircraft’s overall weight, they become more fuel efficient.
Environmental Considerations: Accordingly, with plastics and composites improving fuel efficiency, they help reduce the environmental impact of aviation by playing a role in the reduction of emissions.
Durability and Strength: Despite being lightweight, many plastics and composites offer high strength-to-weight ratios, which makes them ideal for structural components and aircraft parts that need to withstand high stresses and forces. Additionally, these materials are resistant to corrosion.
Design Factors: These materials can be molded into complex shapes with varying geometries. This flexibility enables engineers to create aerodynamic and efficient aircraft shapes.
Maintenance Reduction: Well-selected plastics and composites are resistant to environmental factors, for example moisture and chemicals, which reduces the need for frequent maintenance. This also leads to lower maintenance costs and less downtime for aircraft.
Noise Reduction: Some composite materials have sound-dampening properties, which can help reduce the noise generated by aircraft; especially important for passenger comfort and noise pollution regulations.
Corrosion Resistance: Unlike metals, plastics and composites used in aviation applications are corrosion resistant, which is particularly significant for aircraft operating in harsh environments or over bodies of saltwater.
With this list of advantages, plastics and composites have been used for various aviation applications, including:
- Ducting and seals for ventilation
- Aircraft doors, external panels and structural reinforcements
- Interior wall panels and luggage storage compartments
- Internal wiring, bushings, and bearings
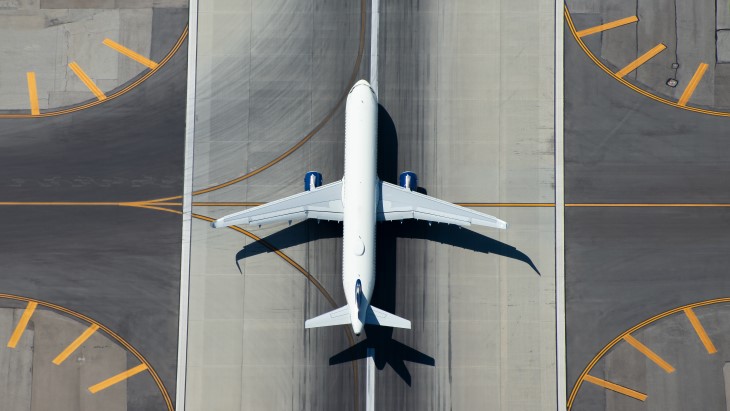
Material Challenges and Innovations
Composites, a combination of different materials to create one with superior properties, have transformed aviation manufacturing. As touched upon, they are the driving force behind the development of aircraft that are not only more fuel efficient but also stronger and more durable.
Fortunately, there continue to be innovations in the production of composite materials, exemplified through the development of high-performance resins and adhesives, carbon fibre-based materials, lightweighting, advanced polymer composites, and more.
High-Performance Resins and Adhesives
High-performance applications are those in which materials, products, or technologies must meet demanding performance criteria. These applications typically require superior performance in terms of speed, efficiency, durability, precision, reliability, or any combination of these factors. In the aviation industry, high-performance products generally have to withstand extreme conditions, such as high temperatures, pressure, and stress, all while maintaining safety and efficiency.
Therefore, a great risk for materials that operate under these conditions is the degradation of their composite layers. Despite that, recent innovations have brought about high-performance resins and adhesives that avert these complications through stronger delamination between the layers.
Carbon Fibre-Based Materials
Commonly used composite materials might not always exhibit the most favorable structural properties for high-performance aviation applications. However, composites made out of carbon-fibre have excellent strength-to-weight ratios, have good impact resistance, have better overall toughness. Additionally, materials composed out of carbon-fibre have exceptional thermal conductivity properties, which makes them ideal for aircraft and aerospace applications.
Lightweighting
To further the advantages of lightweight materials in aviation structures, material innovations such as carbon fiber-reinforced polymers (CFRP) and foam core composites have been on the rise. These material advancements also ensure that structural integrity and performance will not be compromised.
Advanced Polymer Composites
To ensure robust connections between the fibers and matrix in composite materials, recent innovations have seen the incorporation of enhanced bonding characteristics in polymer matrices. Therefore, more effective bonding can occur between a polymer matrix and reinforcement fibers, which increases overall material strength and durability.
Optimizing Plastics and Composites Use for the Aviation Industry
Besides innovations in material production, technological solutions, like sensXPERT Digital Mold, are capable of optimizing plastics and composite part manufacturing. In the case of Digital Mold, this is achieved through the characterization of in-mold material behavior using dielectric analysis, machine learning, and material models.
sensXPERT collects critical process data, including flow front, degree of cure, glass transition temperature, and viscosity, to train the models and generate live forecasts on material behavior within a curing cycle. Therefore, manufacturers who are equipped with Digital Mold gain greater material insights, particularly in relation to their processes, which enables enhanced process control, increased productivity, and overall efficient production.
Next week, we will be examining the most common composite manufacturing processes in the aerospace industry and expanding upon the relevance of sensXPERT for aerospace manufacturers.
If you are eager to learn more about our solution, you can visit our ‘How it works’ page.