The Interplay of Economic Efficiency and Energy Savings in Plastics Manufacturing
The two pursuits of economic efficiency and energy conservation are anchors in the plastics industry’s path towards a more sustainable, cost-effective future. Especially amongst a growing demand for streamlined processes and environmentally conscious production practices, plastics manufacturers find themselves divided by a desire to innovate and to carry out responsible production.
This article investigates this interplay between economic efficiency in production and energy savings. Instead of seeing the objective of conserving energy as a liability to increased economic efficiency, we examine how minimizing energy consumption can actually maximize a plastics manufacturer’s economic efficiency.
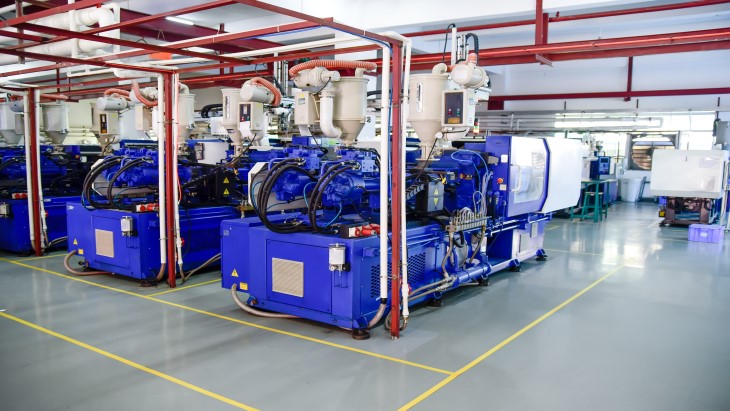
A new era of smart manufacturing, led by the development of Industry 4.0 technologies, has opened opportunities for optimized plastics production processes, reduced energy consumption, and significant returns on investment.
Throughout this article, we will address the current challenge of high energy consumption in the manufacturing landscape, along with its economic implications. We will then introduce the role of process optimization and dynamic process adjustment in increasing energy savings in manufacturing. Finally, we will delve into how sensXPERT’s process optimization solution propels energy efficiency and cost savings in plastics manufacturing processes.
The Economic Implications of High Energy Consumption in Plastics Manufacturing
The production of plastic parts often involves complex processes such as extrusion, injection molding, resin transfer molding, and more, all of which demand substantial energy inputs. Energy-intensive manufacturing leads to several challenges that are felt beyond the production floor.
Mounting Operational Costs
High energy consumption directly translates into rising operational costs for plastics manufacturers. The energy-intensive nature of polymer processing augments the need for electricity, which significantly contributes to a large portion of overall production costs. As energy prices fluctuate globally, plastics processors can find themselves vulnerable to economic uncertainties.
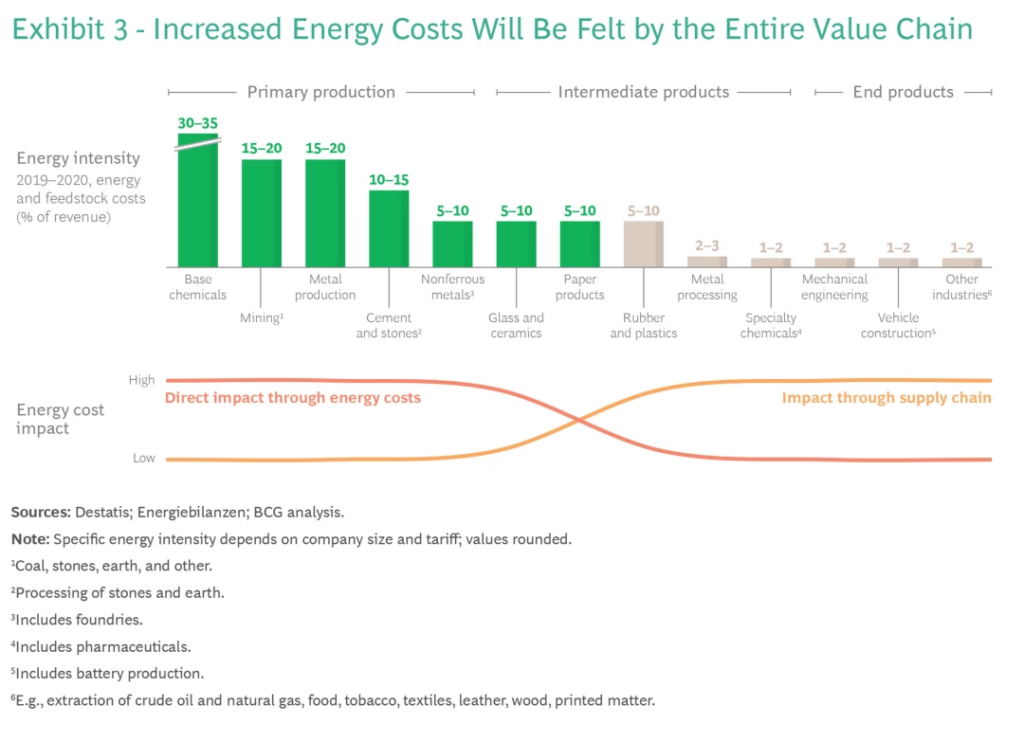
Sustainability Concerns
Heightened energy usage has a substantial impact on the plastics industry’s carbon footprint and raises concerns regarding climate change and resource depletion. The growing demand for sustainable practices has led to the adoption of several environmentally conscious regulations, including the EU Green Deal. Therefore, manufacturers are expected to adopt eco-friendly practices, which in turn necessitates a balance between economic efficiency and environmental responsibility.
Regulatory Compliance and Market Access
Sustainability concerns are, as touched upon, directly tied to global environmental regulations. For plastics manufacturers, that means they are obligated to comply with stringent energy efficiency standards in their production. Should they fail to comply with these regulations, they may face legal consequences and market access restrictions.
Competitive Disadvantages
Besides market access restrictions, manufacturers grappling with high energy costs risk losing their competitive edge. Companies that optimize energy consumption and reduce overall production expenses gain an advantage in their ability to adapt to evolving market dynamics.
Rising operational costs, sustainability concerns, regulatory compliance, market access restrictions, and competitive disadvantages are just a few of the challenges that plastics manufacturers may face if they are cost and energy inefficient.
So, how can plastics manufacturers minimize their energy consumption to maximize their economic efficiency? Process optimization and dynamic process adjustment play a great role in propelling manufacturers both economically and sustainably.
Reducing Energy Consumption Through Process Optimization
In their goals of saving costs and upholding their environmental responsibilities, plastics manufacturers are increasingly turning towards innovative process optimization techniques to reduce energy consumption. Process optimization combined with dynamic process adjustment are crucial tools for manufacturers seeking to achieve energy efficiency without compromising product quality.
Process optimization involves a detailed examination of every component in the plastics manufacturing process, from raw material input to the final product. By fine-tuning parameters such as temperature, pressure, and cycle times, plastics processors can achieve optimal energy savings.
Real-time process monitoring is highly valuable in process optimization. With the close tracking of factors such as material viscosity, temperature fluctuations, and pressure levels, operators can make prompt informed decisions and immediately adjust cycles accordingly. This approach ensures that energy will be applied precisely where and when it is needed.

At the same time, the abovementioned challenges tied to high energy consumption can all be combatted by introducing process optimization techniques into the plastics manufacturing process. As companies invest in energy-efficient technologies and practices, they reduce their operational expenses. The money saved on energy bills and associated costs translates into improved profitability and a positive impact on return on investment.
Additionally, optimizing processes leads to minimized resource consumption, including energy and material waste, which reduces a company’s overall environmental impact. This aligns with sustainability goals and compliance with environmental regulations.
Process Optimization with sensXPERT
sensXPERT provides a state-of-the-art process optimization solution that enables real-time monitoring and dynamic process control. sensXPERT Digital Mold utilizes material characterization sensors that measure in-mold material behavior in real-time.
Furthermore, predictive algorithms on sensXPERT’s accompanying edge device forecast the point at which a material will have reach the desired degree of cure or crystallization. Therefore, the process cycle can be ended or extended depending on material’s curing progression. This diminishes the need for lengthened cycles as ‘safety buffers’ and reduces the typical amount of energy spent on a cycle.
All in all, sensXPERT Digital Mold creates process transparency and wields data-driven predictions to optimize cycle times, minimize energy consumption, and save costs.
How can sensXPERT impact your energy consumption and economic efficiency?
To determine just how much of an increase in economic efficiency and return on investment sensXPERT Digital Mold can bring to your business, use our free ROI Calculator. Discover the potential savings you can generate from reduced cycle times, waste, and downtime by integrating sensXPERT into your production.