Maximizing Production Outcomes for Plastics Manufacturers
sensXPERT enables manufacturers to boost efficiency in their production processes. With in-mold sensors and advanced data analytics, our solution delivers real-time insights into material behavior, optimizing cure cycles, reducing scrap, and achieving precise crystallization. This not only improves operational efficiency but also contributes to resource conservation and waste reduction. Our commitment to innovation aligns with the evolving landscape of responsible manufacturing, empowering plastics companies to achieve higher standards of environmental and operational excellence.

Key benefits of our solution:
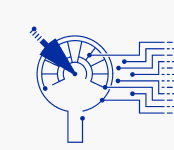
Cost-effectiveness and more sustainable production
By leveraging valuable, real-time data, sensXPERT predicts the exact point in time at which each part will reach its optimal degree of cure or crystallization. This makes dynamically adapting your manufacturing process according to evolving conditions inside and outside the mold a reality! The result: more effective cycle times, increased production efficiency, greater energy savings, and less scrap.
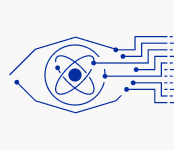
Holistic production control and transparency
Ordinarily, quality control in manufacturing occurs during post-process quality assurance tests. These tests often take a sample out of a batch of finished products and dismantle the sample of products to check for defects, structural weaknesses, performance issues, and more. Fortunately, with sensXPERT’s in-mold dielectric sensors, real-time transparency allows you to conduct quality control during the processing of each part, without having to break down any final parts. sensXPERT also ensures that any potential defects will be avoided through adaptive process control.

Dependability in manufacturing operations
Ensure reliability in your composite manufacturing processes with our innovative solution. Real-time monitoring and analysis of critical parameters empower you to maintain precise control, detect defects early, and deliver consistent, high-quality products. Optimize your processes, reduce waste, and exceed customer expectations with our reliable solution.
The sensXPERT solution












sensXPERT’s material characterization sensors wield dielectric analysis to measure real-time, in-mold material behavior. The sensors are compatible with a wide variety of materials, such as thermosets, thermoplastics, fiber-reinforced polymers, elastomers, and sands or stones bonded with resins.
By calculating the degree of cure, degree of crystallization or vulcanization during the production process, sensXPERT is capable of detecting material deviations in real time.
The sensors are robustly engineered to withstand molding pressures and temperatures.
The material characterization sensors can be integrated into processes such as (Reaction) Injection Molding, Thermoforming and Compression Molding, Transfer Molding, Vacuum Infusion, and Autoclave Curing.
Designed to be robust and durable in manufacturing environments, the sensXPERT Edge Device bridges the physical and digital worlds of polymer processing. The edge device is a powerful industrial personal computer (IPC) and dielectric analyzing system that is loaded with machine learning algorithms and offers cloud connectivity.
As the single source of truth, the sensXPERT Edge Device communicates directly with the machine, exchanging manufacturing parameters and material properties, whilst sending and receiving trigger signals.
Advanced onboard machine learning models power sensXPERT’s dynamic and adaptive process control capabilities in the face of unforeseen changes in production, for example material aging, humidity, temperature, etc.
The edge device is not only compatible with sensXPERT’s material characterization sensors, but it can also connect to and receive real-time data from third-party pressure and/or temperature sensors.
The sensXPERT WebApp enables machine operators to monitor and optimize the manufacturing process in real time.
This interface visualizes the full spectrum of process and material parameters for every product being manufactured.
The WebApp also visualizes the advanced machine learning models in action. Machine learning models accurately predict the degree of cure/crystallization, glass transition temperature, and other thermal/mechanical material properties.
By presenting these real-time predictions on the edge device interface, operators are enabled to confidently optimize their processes right away, ensuring quality control in the manufacturing of each part.
The sensXPERT Digital Cloud Service collects and stores all measurement data via REST API and is the central collection site for all process data I.e., through an OPC-UA connection.
In the Cloud, data associated with quality indicators are processed and calculated for every part produced.
Selected parameters are visualized in sensXPERT’s Digital Cloud Service, displaying trends and deviations.
Easy-to-access dashboards offer an overview of all edge devices installed across multiple sites and/or production lines in your plastics manufacturing. These dashboards also inform manufacturers of any opportunities for optimization.
Your Return of Investment
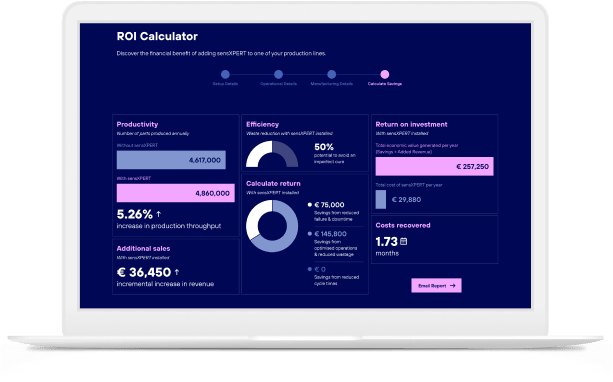
ROI Calculator
Calculate the real value of sensXPERT for your manufacturing business
Considering sensXPERT for your business? Use our powerful ROI calculator and see how much of a return this could make for your business.
Launch ROI calculatorUp to 50% reduction
of the existing rate of scrap produced

Up to 23% increase
in energy savings

Up to 30% reduction
in length of manufacturing cycle times

Additional Relevant Resources
October 14, 2024
Quality and Efficiency in Aviation: The Technology That Learned to Control
How does a cutting-edge measurement technology evolve into a solution that drives real-time insights and transforms quality control and efficiency in aviation manufacturing?
September 4, 2024
Escape the Status Quo with Cutting-Edge Plastics Process Optimization
Explore how to overcome the top concerns in plastics process optimization and turn hesitation into innovation and efficiency.
September 2, 2024
Overcoming 5 Key Obstacles to Plastics Process Success
Download our eBook to discover how you can turn these common concerns into opportunities for growth and innovation in your plastics manufacturing processes.