What is Polyurethane? A Materials Case
Polyurethane is an adaptable class of polymers that is used to combat difficulties or challenges in a myriad of industrial and consumer products. The material’s versatility allows it to insulate sensitive components, provide consumer comfort, and resist harsh environmental conditions. Polyurethane can also be molded into numerous sizes and shapes.
We outline what polyurethane is, the properties exhibited by the materials, the applications in which this material is applied, and provide a materials case on polyurethane conducted by sensXPERT’s applications specialists.
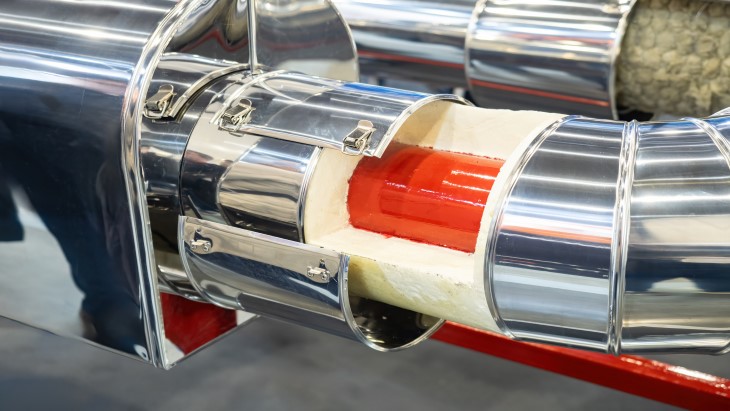
What is Polyurethane?
This versatile class of polymers is formed through a reaction between isocyanates and polyols. Polyurethanes (PU), can be rigid and hard or flexible and soft depending on the chemical formulation and production process. PUs have a vast range of properties that make them popular in numerous applications.
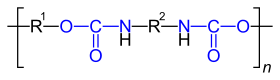
During formation, polyurethanes commonly undergo a reaction called polyurethane polymerization. In the formation process, isocyanates react with polyols to form urethane linkages, and material suppliers can adjust this reaction to influence the hardness, flexibility, or other properties of the final polyurethane material.
Property | Polyurethane (PU) | Other Plastics |
---|---|---|
Flexibility | Variable, depending on formulation | Often limited |
Heat Resistance | Very high | Depends on material type |
Application Possibilities | Versatile in industry & consumer goods | Mostly specific applications |
Processing | Injection molding, potting, coatings | Variable, but often complex |
Table: Polyurethane (PU) vs. other Plastics
Material suppliers produce polyurethanes that exhibit various properties, some of which include the following:
Property | Description |
---|---|
Durability | Polyurethanes are highly durable and resistant to external influences. |
Versatility | Can be formulated to be either rigid or flexible and used in various industries. |
Water Resistance | Resistant to moisture, making it ideal for use in humid environments. |
Chemical Resistance | Resistant to many harsh chemicals and solvents. |
Table: Properties of Polyurethane
Accordingly, there are several types of polyurethanes that are chosen for different applications:
Polyurethane Type | Application |
---|---|
Flexible Foams | Used in comfort applications such as cushions, car seats, and mattresses. |
Rigid Foams | Used as insulation in construction and household appliances. |
Coatings | Provides protective coatings for surfaces like metal, concrete, or wood. |
Adhesives and Sealants | Used for bonding or sealing applications. |
Elastomers | Exhibit rubber-like properties and are used in applications such as wheels, seals, or tires. |
Table: Types of Polyurethane and Their Applications
Besides the above-mentioned applications, polyurethane is often used in electromobility and electronics manufacturing to insulate components against harmful influences.
What is Potting?
Potting is a process wielded in manufacturing to encapsulate or embed components or devices in protective materials. Potting is conducted to provide mechanical support, environmental protection, and, in some cases, insulation for enclosed items. This process is typically carried out to safeguard components from environmental factors such as moisture, vibrations, thermal stress, and more.
Potting is concerned with the pouring or dispensing of a potting material around components in an open mold or enclosure.
Potting Method | Characteristics | Typical Applications |
---|---|---|
Open Potting | Material is poured around the component | Protection of circuits, LED components |
Closed Potting | Component is placed into a cavity and sealed | High-performance electronics, industrial sensors |
Table: Comparison: Open vs. Closed Potting
Potting vs. Coating
Potting and coating are two distinct methods used to protect components. In potting, the entire component is embedded in a specialized material, fully encapsulating it. This provides comprehensive protection against moisture, chemical exposure, mechanical stress, and temperature fluctuations.
In contrast, coating forms only a thin protective layer on the surface of the component. While it also shields against external influences, it does not offer the same level of protection as potting. Coatings are primarily used in applications with lower protection requirements, whereas potting is particularly suitable for sensitive electronic components or parts exposed to extreme conditions.
Potting vs. Encapsulation – Key Differences
Potting and encapsulation are both methods for protecting electronic components, but they differ in their application and the degree of protection they offer.
In potting, the material is poured into an open mold or enclosure, surrounding and safeguarding the components. This ensures mechanical stability and protection from external factors such as moisture, vibrations, and temperature fluctuations.
Encapsulation, on the other hand, involves placing electronic components into a closed mold or cavity and then enclosing them with encapsulating material. This results in complete isolation of the component, offering even greater protection from environmental influences. Encapsulation is commonly used in applications that require exceptional resistance to chemical, electrical, or mechanical stress.

You can read more about electronics encapsulation by downloading our free white paper on ‘A Guide to Electronics Encapsulation: Optimizing Closed Mold Encapsulation Processes’.
A Materials Case: Potting Polyurethane
Depending on the type, polyurethane reacts extremely quickly at room temperature. In this case, sensXPERT’s applications specialists conducted material trials on rigid foam polyurethane to determine the material’s behavior throughout its reaction process.
More specifically, the rigid foam PU is a foam with gas bubbles that, once cured, cannot be deformed. This material is desirable for several applications because the gas bubbles ensure that the final component’s overall weight will be lighter than if compact materials were used.
The sensXPERT specialists conducted the trials with the aim of understanding the most effective ways of using the sensXPERT Insight dielectric sensor technology to characterize polyurethane behavior in a potting process.
To begin with, the specialists selected a couple of processing temperatures to examine whether polyurethane displays different molecular behavior when subjected to different temperatures. Additionally, sensXPERT’s material specialists monitored the effects on the measurements when adding a thin film – teflon foil, to be specific – between our sensor technology and the polyurethane.
Trial Results
The polyurethane material study led to several findings. Regarding the impact of placing a thin film between sensXPERT’s dielectric sensors and the polyurethane, our specialists concluded that there are no detrimental effects on the measurements.
Figure 1 illustrates the curing progression of polyurethane at 45°C with a teflon foil film. These results are noteworthy, as, due to polyurethane’s adhesive properties, some manufacturers may want to use a thin film to prevent the material from sticking to their molds, which does not hamper the dielectric sensors from conducting real-time material measurements.
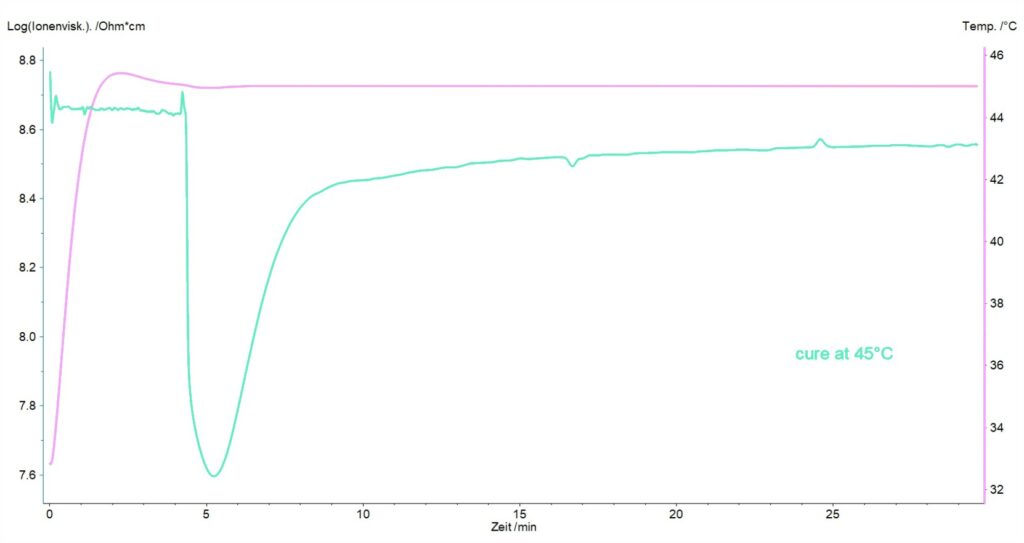
Additionally, results of the material study concluded that as the material is heated, molecular mobility increases and viscosity decreases. This influence is more pronounced at higher temperatures, as is visible in figure 2 with a greater drop in ion and rheological viscosity at 45°C (green line). At a certain point, the curing reaction begins and there is an initial balance between the drop in viscosity and curing with the curing reaction eventually overtaking the drop in viscosity.
Another conclusion by our specialists is that polyurethane curing reactions are quicker at higher temperatures.
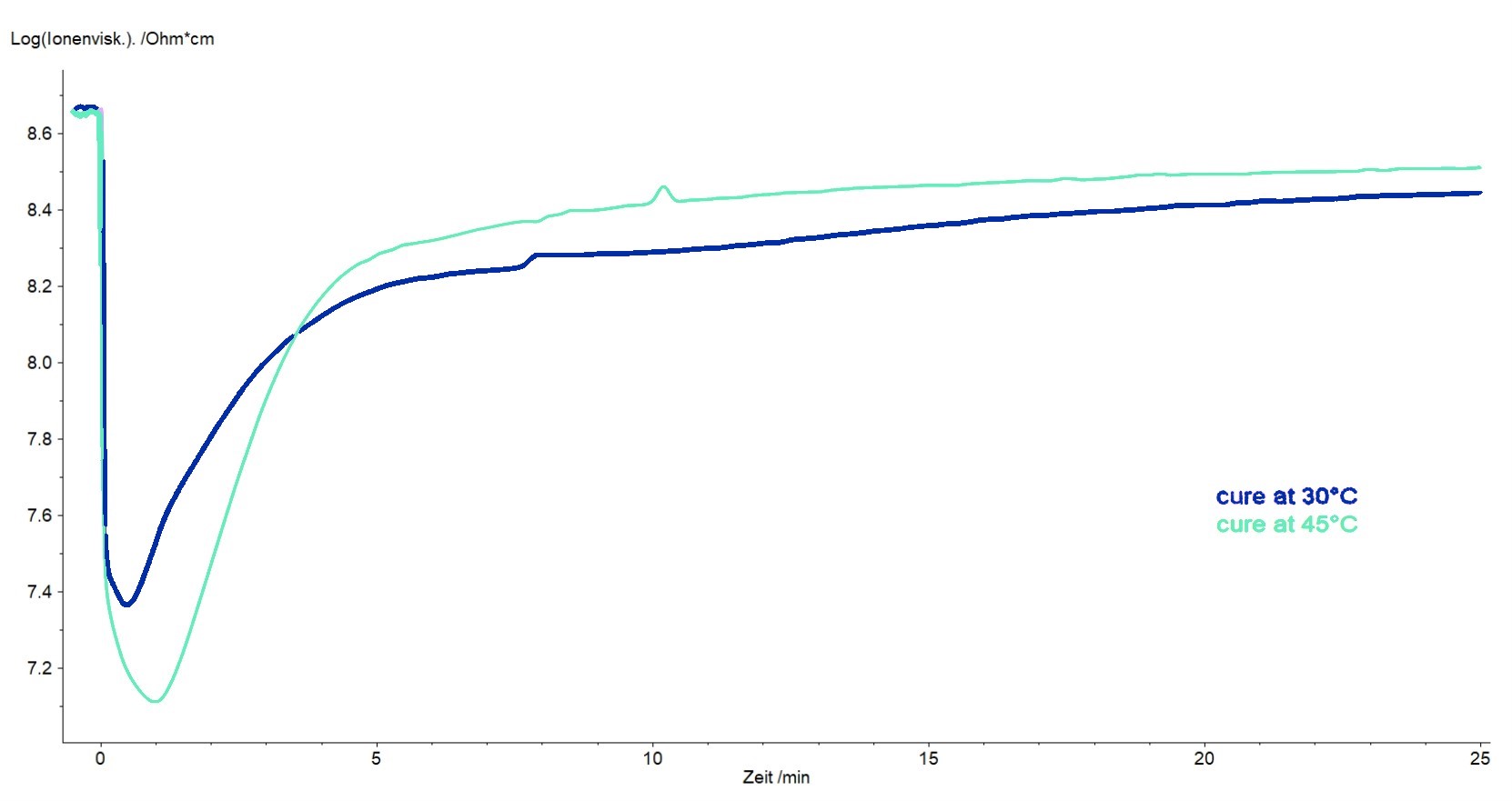
Finally, figure 3 presents the polyurethane’s relative permittivity, which indicates the extent to which a material can be polarized. The measurement technology, in this case, measures dipole mobility and examines the PU’s foaming process. The initial drop in figure 3 represents the start of the material’s foaming reaction.
The foaming reaction is a crucial one to monitor because the amount and size of the gas bubbles within the foam can heavily impact final component performance. By monitoring the real-time foaming reaction, manufacturers can adjust their process parameters to achieve their desired foaming behavior.
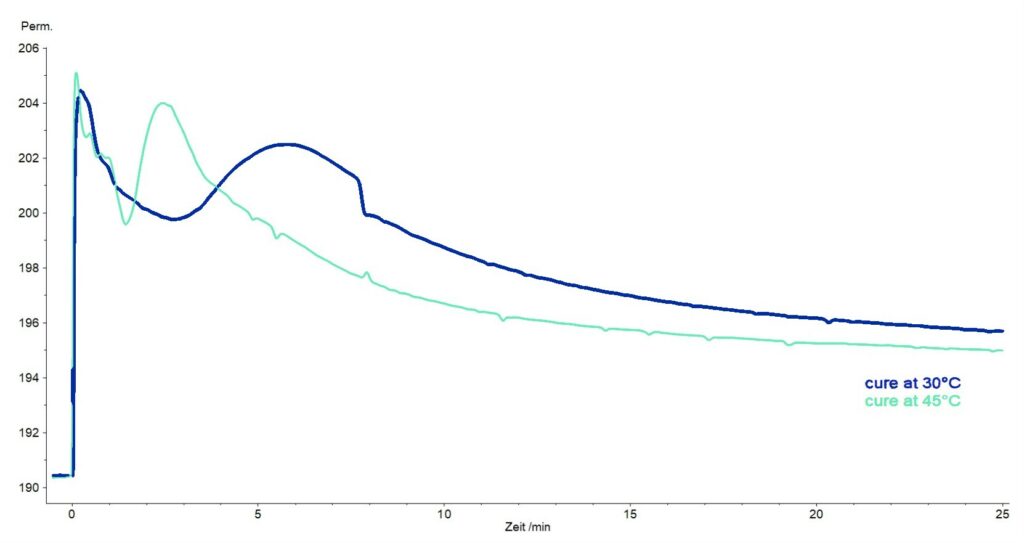
Overall, our technology ensures that material behavior is sufficiently monitored in real-time to aid manufacturers in achieving their desired degrees of cure and making sure that their final components possess the properties required for their targeted applications.
By understanding material behavior, manufacturers gain real-time insights on the quality of their final components, without needing to conduct downstream quality assurance testing.