Kunststoffverarbeiter, insbesondere solche, die mit duroplastischen Werkstoffen arbeiten, haben im Allgemeinen wenig Einblick, was während des Verarbeitungszyklus tatsächlich im Werkzeug passiert. Auch Weiterverarbeiter, die ein Teil mit einer duroplastischen Schutzschicht umspritzen, stehen vor dieser Herausforderung.
Daher ist es schwierig festzustellen, ob die gefertigten Teile den Spezifikationen entsprechen, ohne dass nachgelagerte Qualitätssicherungsprüfungen (QA) durchgeführt werden. Ohne einen ausreichenden Einblick in die Auswirkungen des Materialverhaltens im Werkzeug auf die Leistung des fertigen Teils haben die Formgeber Schwierigkeiten, ihre Prozesse zu steuern und in Echtzeit auf Prozessabweichungen zu reagieren. Dies kann zu übermäßig langen Zykluszeiten, einem hohem Energieverbrauch, hohen Ausschussraten und hohen Qualitätskosten führen.
Ein neues im Werkzeug integriertes Prozessüberwachungssystem der NETZSCH Process Intelligence GmbH, das sensXPERT Digital Mold, ermöglicht jetzt jedoch Echtzeiteinblicke in den Verarbeitungsprozess. Durch den Einsatz von Maschinenlern-(ML-)Algorithmen ist sensXPERT in der Lage, das Materialverhalten genau vorherzusagen, was den Herstellern hilft, ihre Prozesse dynamisch zu steuern und eine konstante Teilequalität zu gewährleisten. Entsprechend unterstützt sensXPERT den Formgeber bei der Reduzierung von Zykluszeiten, Energieverbrauch, Ausschussraten und Kosten.
Um den Wert von sensXPERT bei der Bewältigung der oben genannten Herausforderungen zu veranschaulichen, stellen wir Ihnen zwei vergleichbare Unternehmen vor, die diese Lösung mithilfe von NETZSCH implementiert haben. Beide Unternehmen verkapseln elektrische Hochspannungskomponenten im RIM-Verfahren (Reaction Injection Molding, Reaktionsspritzgießen). Sie unterscheiden sich durch die verwendeten Polymere und die von ihnen hergestellten Teile. Beide stehen jedoch vor ähnlichen Herausforderungen wie hohen Ausschussraten und hohen Qualitätskosten aufgrund mangelnder Transparenz während des Formgebungsprozesses. Diese Fallstudie zeigt die Fähigkeit von sensXPERT, die Transparenz zu erhöhen und Prozesse zu verbessern, selbst wenn die technische Integration noch nicht abgeschlossen ist.
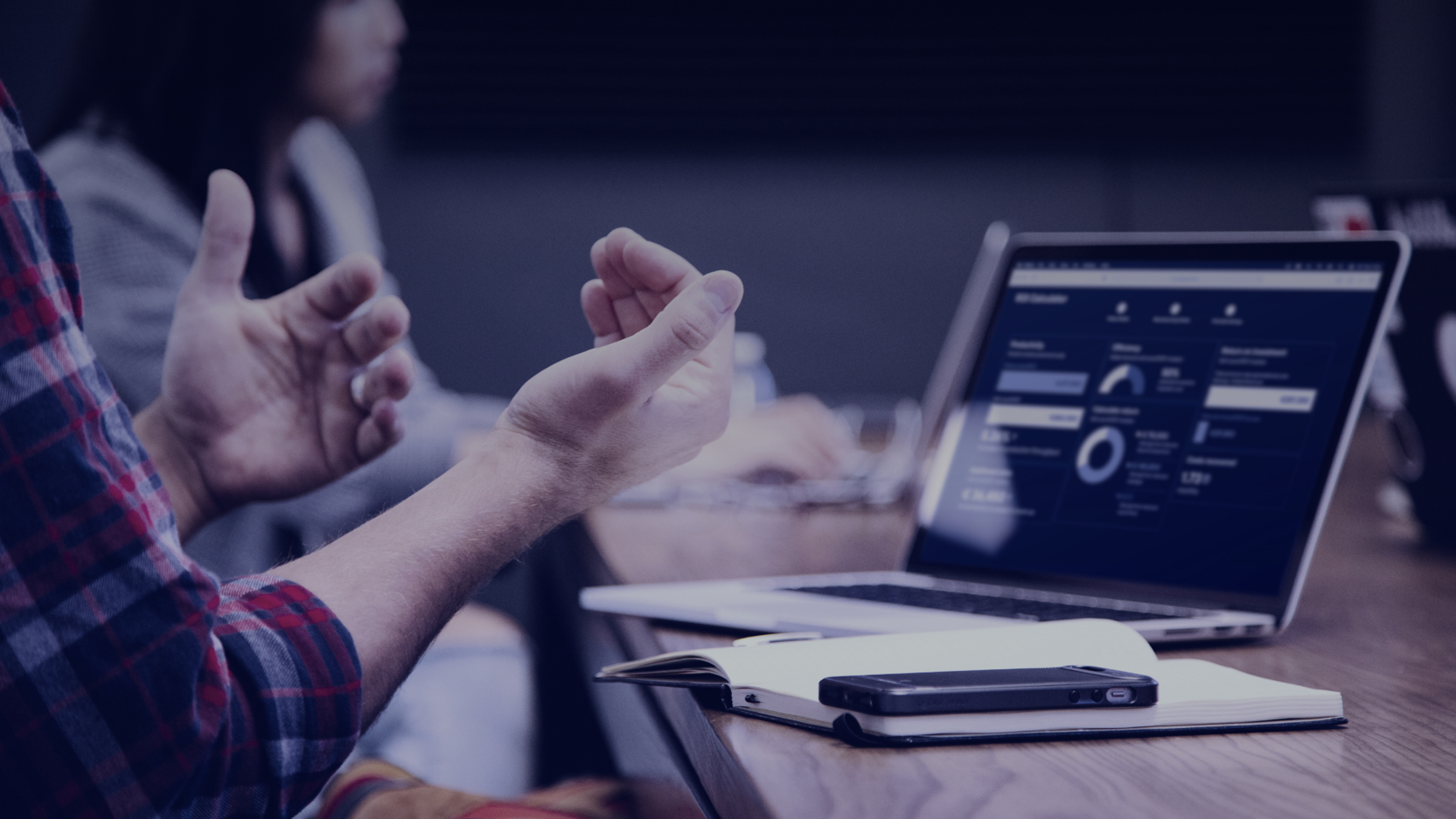
Einblicke in das Material
Unternehmen A und Unternehmen B stellen Funktionsteile für Hochspannungsanwendungen wie Stromversorgungslösungen her. Unternehmen A stellt Steckverbinder her, während Unternehmen B Buchsen fertigt.
Unternehmen A verarbeitet Ethylen-Propylen-Dien-Monomer-(EPDM-)Kautschuk in einem RIM-Verfahren. Dieser synthetische Kautschuk ist bekannt für seine Haltbarkeit, Abrieb- und Reißfestigkeit sowie seine hervorragende Metallhaftung und Flexibilität. Darüber hinaus ist EPDM gegen die meisten Chemikalien auf Wasserbasis, polare Lösungsmittel und Lösungsmittel bei erhöhten Temperaturen beständig. EPDM bietet auch eine hervorragende Beständigkeit gegen Alterung durch Hitzeeinwirkung, UV-Strahlung, Witterungseinflüsse und Ozon. Es kann eine sehr glatte geformte Oberfläche erzeugen. Das Material eignet sich aufgrund seiner geringen elektrischen Leitfähigkeit besonders für die elektrische Isolierung.
Unternehmen B nutzt ebenfalls ein RIM-Verfahren, verwendet aber Epoxidharz zur Herstellung seiner Teile. Epoxidharze sind für ihre hervorragende Zug-, Druck- und Biegefestigkeit bekannt. Sie sind außerdem stoß- und abriebfest, ermüdungsbeständig, feuchtigkeits- und dampfbeständig sowie weitgehend chemikalien-, strahlungs- und korrosionsbeständig. Darüber hinaus weist das Material eine geringe Schrumpfung nach dem Aushärten (1 %) und eine hohe Wärmeverträglichkeit (bis zu 190 °C) auf. Epoxidharze bieten eine ausgezeichnete Haftung auf verschiedenen Füllstoffen, Verstärkungsmitteln und Substraten. Ähnlich wie EPDM bieten auch Epoxidharze eine hohe elektrische Isolierung. Dadurch eignen sie sich hervorragend zur Verwendung in Motoren, Generatoren, Transformatoren, Getriebeschaltern, Buchsen, Isolatoren, Leiterplatten, Vergussmassen und Halbleiterverkapselungen.

Allgemeine Herausforderungen
Beide Unternehmen stehen bei ihrem Anliegen, die Transparenz während des RIM-Verfahrens zu steigern, vor ähnlichen Herausforderungen. Aufgrund der mangelnden Transparenz können beide Unternehmen während des Formgebungszyklus nicht wissen, ob sie gute oder schlechte Teile fertigen. Aus diesem Grund ist es schwierig, die Korrelation zwischen dem Materialverhalten während der Formgebung und den Fehlern zu verstehen, die während der nachgelagerten Qualitätsprüfung entdeckt werden. In den vorliegenden Fällen handelt es sich um ein defektes Teil, das eine eingehende Qualitätsprüfung nicht bestehen würde. Ein zusätzliches Anliegen ist die Fähigkeit, mögliche Verunreinigung des Materials während der Verarbeitung zu erkennen.
Schwierigkeiten bei der Transparenz und der Qualitätskontrolle nach der Verarbeitung können zu hohem und kostspieligem Ausschuss führen. Die Vorwegnahme und Reduzierung dieses Ausschusses würde die Nachhaltigkeit der Fertigung verbessern. Das Ziel beider Unternehmen ist es, Prozesstransparenz zu schaffen, die Prozessstabilität zu verbessern, die Qualität zu steigern und die Kosten zu senken.
Wie kann sensXPERT dabei helfen?
Die Unternehmen haben sich an das Team von NETZSCH Process Intelligence gewandt, um die Qualitätskontrolle zu verbessern, die Ausschussrate zu reduzieren und die Auswirkungen der Verarbeitung auf die Leistung des fertigen Teils besser zu verstehen. Außerdem wollten sie herausfinden, ob die sensXPERT-Technologie Fehler in fertigen Teilen erkennen und reduzieren kann. Das System verfolgt oder misst zwar nicht direkt Defekte, aber es bildet das Materialverhalten und die Veränderung während der Aushärtung ab. Die daraus abgeleiteten Einblicke helfen Kunststoffverarbeitern, die Vorgänge im Werkzeugs besser zu verstehen, Fehlerursachen schneller zu erkennen und Prozesse zu optimieren, um gleichbleibende Qualitätsergebnisse zu gewährleisten.
Das sensXPERT-System umfasst speziell entwickelte und hergestellte gehärtete dielektrische Sensoren, die in einem Werkzeug am Beginn des Durchflusses, in der Nähe oder am Anschnitt und am Ende des Durchflusses angebracht werden. Das System misst kritische Material- und Prozessparameter, die während des gesamten Formgebungszyklus im Werkzeug auftreten, einschließlich:
- Aushärtungsgrad (Degree of Cure; DoC),
- Grad der Polymerisation,
- Glasübergangstemperatur (Tg),
- Viskosität und Position der Fließfront,
- Temperatur im Werkzeugs und
- Materialabweichungen (z. B. aufgrund von Alterung, nicht spezifikationskonformem Material oder Verunreinigungen, z. B. recyceltes Material oder metallische Einsätze, die nicht vollständig von Spänen gereinigt wurden).
Das sensXPERT Edge-Gerät, ein gehärteter PC ohne Tastatur und Monitor, befindet sich außerhalb des Werkzeugs, aber in unmittelbarer Nähe der Presse und ist mit den dielektrischen Sensoren fest verdrahtet. Eine WebApp, die als Schnittstelle des Edge-Geräts fungiert, ermöglicht es den Herstellern, ihre Prozessparameter in Echtzeit effektiv anzupassen. Diese Schnittstelle visualisiert laufende Prozesse und bietet den Bedienern mit Hilfe von Vorhersage-Algorithmen einen optimalen Aushärtungspunkt. Die Daten auf dem Edge-Gerät werden nach einem Fertigungszyklus an das Konto des Kunden im sensXPERT Cloud Service übertragen. In der Cloud werden die Daten analysiert und mit allen zuvor erfassten Daten verglichen, um bestimmte Qualitätsindikatoren zu beurteilen.
Zur dynamischen Steuerung von Prozessen und zur Sicherstellung der Teilequalität werden historische Daten verwendet, um ML-Algorithmen zu trainieren. Das sensXPERT System kann auch Sensordaten von Drittanbietern, wie z. B. Werkzeugtemperatur, -druck und -feuchtigkeit, berücksichtigen, die ebenfalls in die ML-Modelle integriert werden können. Die trainierten und neu trainierten Algorithmen helfen, die Vorhersagen der Prozessergebnisse kontinuierlich zu verfeinern. Auf der Grundlage der Vorhersagen kann ein Techniker entscheiden, ob er eine Prozesseinstellung ändern sollte oder nicht.
Nach der vollständigen Installation des sensXPERT-Systems können Unternehmen besser nachvollziehen, ob die Materialhandhabung vor der Verarbeitung zu Abweichungen in der Fertigung beiträgt. Außerdem erhalten sie einen besseren Einblick in die Auswirkungen des Aushärtungsvorgangs auf die endgültigen Teileigenschaften und wie dies zu Qualitätsmängeln beitragen kann.
Vorläufige Ergebnisse
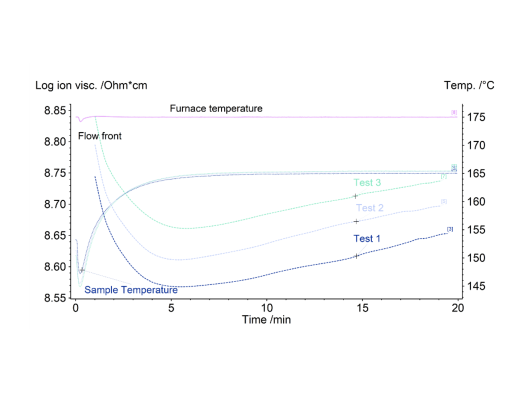
Auf der Grundlage der bekannten Materialeigenschaften von EPDM-Kautschuk lassen die vorläufigen Ergebnisse darauf schließen, was während der Formgebung geschieht. Wenn das Material erwärmt wird, sinkt seine Viskosität und der Fluss nimmt zu, was durch die Ionenviskosität (in Ohm-cm) angezeigt wird. Dies entspricht der Bewegung des Materials. Wenn die Temperatur jedoch weiter ansteigt, tritt Vernetzung auf. Dies erhöht die Viskosität und verringert die Mobilität der Ionen, was auf eine Verlangsamung des Flusses schließen lässt. Folglich kann die Messung eines Prozessparameters wie der Ionenviskosität unter anderem Aufschluss über den Grad der Aushärtung geben.
Anhand von Materialcharakterisierungs- und Verarbeitungstestläufen in einem mit Instrumenten ausgestatteten Werkzeug wird dann untersucht, ob der Grad der Aushärtung die kritische Eigenschaft ist, die sich darauf auswirkt, ob verkapselte Teile die Qualitätssicherungsprüfung bestehen oder nicht.