15% Zykluszeitverkürzung bei der Herstellung von Gummistatoren bei NETZSCH Pumpen & Systeme
Das Wichtigste im Überblick

Hohe Marktnachfrage erhöht den Druck auf Hersteller, ihre Prozesse zu optimieren und die Produktivität zu steigern. Als solche versuchen Hersteller, die Zykluszeiten zu verkürzen, während sie gleichzeitig die Qualität des Endprodukts erhalten.
NETZSCH Pumpen & Systees stellt Exzenterschneckenpumpen her, wobei eine Hauptkomponente Gummistatorpumpen sind. NETZSCH Pumpen & Systeme arbeitete mit sensXPERT zusammen, um die Zykluszeiten zu verkürzen und die Prozesseffizienz bei der Herstellung der Gummistatorpumpen zu steigern.
Erste Ergebnisse zeigen das Potenzial für eine 15%ige Reduzierung der Zykluszeit durch die Implementierung von sensXPERT in einem Produktionsprozess für Gummistatorpumpen bei NETZSCH Pumpen & Systeme.
Die globale Pumpenherstellungsindustrie ist in den letzten Jahren allmählich gewachsen. Die steigende Nachfrage aus den Bereichen Energie, Öl und Gas, Wasser und Chemie hat die Entwicklung effizienterer Pumpen und Systeme vorangetrieben, die verschiedene Stoffe wie Schlämme, Flüssigkeiten und Gase zuverlässig fördern können. Im Jahr 2021 wurde der Markt für industrielle Pumpen auf etwa 70 Milliarden US-Dollar geschätzt und soll bis 2025 auf 90 Milliarden US-Dollar steigen.
Pumpen, insbesondere industrielle Pumpen, finden Anwendungen in verschiedenen Branchen: Wasser- und Abwasserwirtschaft, Chemie, Umwelt und Energie, Batterie, Öl und Gas, Lebensmittel und Getränke, Energieerzeugung und Bauwesen, um nur einige zu nennen. Aufgrund der hohen Nachfrage nach effizienten und robusten Pumpen müssen Hersteller sicherstellen, dass ihre Produktionsprozesse optimiert sind und mit Mitbewerbern konkurrieren können.
Bei ihren Bemühungen, die Produktivitätsniveaus zu verbessern und den hohen Anforderungen gerecht zu werden, können Hersteller auf mehrere Herausforderungen stoßen, die sie daran hindern könnten, ihre Ziele zu erreichen. Eine solche Herausforderung besteht darin, dass lange Zykluszeiten erforderlich sind, um eine ausreichende Aushärtung oder Vulkanisation der Teile sicherzustellen, wobei jedoch eine beträchtliche Menge an Energie und Zeit verloren geht.
Die Implementierung von Prozesssteuerungslösungen, die Transparenz bieten und eine dynamische Prozessanpassung ermöglichen, ist jedoch ein wertvoller Weg, um dieser Schwierigkeit zu begegnen. Dieses Anwendungsbeispiel wird das Potenzial von materialbasierten dynamischen Zykluszeiten zur Steigerung der Prozesseffizienz bei NETZSCH Pumpen & Systeme mit sensXPERT Insight, integriert in deren Fertigung, aufzeigen.
Über NETZSCH Pumpen & Systeme
Mit Anwendungen in den oben genannten Branchen fertigt und vertreibt NETZSCH Pumpen & Systeme seit über 70 Jahren eine breite Palette von Pumpenlösungen. Von Mehrspindelpumpen bis hin zu Drehkolbenpumpen bietet NETZSCH Pumpen & Systeme eine Vielzahl von Lösungen für jeden Anwendungsbereich.
Im vorliegenden Fall arbeitete NETZSCH Pumpen & Systeme mit sensXPERT zusammen, um Optimierungsmöglichkeiten in einem ihrer Elastomerverarbeitungsprozesse zu ermitteln und umzusetzen. Der spezifische Pumpenherstellungsprozess, der untersucht wurde, war der des NEMO®-Exzenterschneckenpumpen.
Was sind Exzenterschneckenpumpen?
Exzenterschneckenpumpen sind Verdrängerpumpen, was bedeutet, dass eine Kraft auf den eingeschlossenen Inhalt der Pumpe ausgeübt wird und ihn mechanisch durch das System vorwärts bewegt. Die Pumpe ist so konzipiert, dass ein Rückfluss des Inhalts vermieden wird. Am häufigsten in Industrien mit schweren Anforderungen eingesetzt, kann die Exzenterschneckenpumpe Medien wie Schlämme und Schlamm fördern, die abrasiv und hochviskos sind. Darüber hinaus ist dieser Pumpentyp in der Lage, schersensitive Materialien zu handhaben.
“Die Hauptkomponenten sind ein rotierender Rotor und ein stationärer [Gummistator]. Der Rotor, auf einer Seite scharnierend oder elastisch befestigt, ist eine runde Gewindeschraube. Auf der Ausgangsseite oszilliert die axiale Position. Der hohle Stator ist elastisch und hat die gleiche Steigungslänge wie der Rotor. Dadurch entstehen Förderräume zwischen Stator und Rotor, die kontinuierlich von der Einlass- zur Auslassseite wandern. Die Größe der Förderräume und die damit verbundene Fördermenge hängen von der Konstruktionsgröße ab. Mit Ausnahme von Rotor und Stator sind alle anderen Komponenten identisch.” [2]
NEMO® Exzenterschneckenpumpe im FSIP®-Design mit xLC®-Statoreinstellungssystem
Insgesamt müssen Pumpenhersteller sicherstellen, dass ihre Produktionsprozesse optimiert sind, um mit den Marktanforderungen Schritt zu halten. In diesem Sinne hat die Zusammenarbeit zwischen sensXPERT und NETZSCH Pumpen & Systeme das bedeutende Potenzial für Zeitersparnis durch die Reduzierung der Zykluszeit aufgedeckt.
Die Herstellung von Gummistatoren für Exzenterschneckenpumpen
Bevor wir uns auf die Zusammenarbeit einlassen, lohnt es sich, den Herstellungsprozess für Exzenterschneckenpumpen bei NETZSCH Pumpen & Systeme genauer zu betrachten.
Während die Exzenterschneckenpumpe, wie bereits erwähnt, aus einem rotierenden Rotor und einem Gummistator besteht, liegt unser Fokus auf der Herstellung des Gummistators.
Zunächst werden dünne Blätter aus synthetischem Gummi in die Spritzgussmaschine gezogen. Der Gummispritzgussprozess beginnt, das gezogene Material wird in einer Schraube plastifiziert und dann in die Form gespritzt. Nach dem Einspritzen in eine beheizte Form vulkanisiert das Material, und der Stator entsteht. Der Stator wird unter Berücksichtigung der Geometrie des Rotors hergestellt, damit ausreichend Platz für die Bildung der Hohlräume vorhanden ist, die während des Pumpvorgangs verschiedene Medien enthalten.
Jede Maschine kann mit verschiedenen Formhohlräumen ausgestattet werden, da sie voneinander getrennt und ausgetauscht werden können. NETZSCH Pumpen & Systeme stellt Statorn von verschiedenen Längen und Durchmessern her, sodass je nach Geometrie des Stators einige Formen unterschiedliche Anzahlen von Hohlräumen haben können. Darüber hinaus variieren die Prozessparameter je nach Geometrie.
Während der Produktion wurden Sicherheitsmargen eingeführt, um einen gewünschten Vulkanisierungsgrad von 90 % zu erreichen, indem die Zykluszeit verlängert wurde. Diese Sicherheitsmargen gewährleisten eine ausreichende Vulkanisierung und stellen sicher, dass das Teil während seiner gesamten Lebensdauer zuverlässig funktioniert.
Der Vulkanisierungsgrad bezieht sich auf die Anzahl der Querverbindungen, die sich zwischen den Molekülen im Gummimaterial gebildet haben, im Verhältnis zu den möglichen Querverbindungen, die entstehen könnten.
Die Messung des Vulkanisierungsgrades ist keine einfache Aufgabe, insbesondere in der Produktion. Heutzutage werden mechanische Gummiprozess-Analysatoren – die großen Rheometern ähneln – verwendet, um den Vulkanisierungsgrad über das Drehmoment zu berechnen, das während der Aushärtung zunimmt. Zusätzliche Messungen werden durch differentielle Scanning-Kalorimetrie (DSC) durchgeführt, das ein Standardinstrument zur Bestimmung der Reaktionswärmeenthalpie ist, sowie zur Berechnung der Aushärtung entsprechend. Da Gummi ein stark gefülltes Polymer ist, mit einer sehr geringen Menge an Wirkstoff, sind DSC-Ergebnisse oft nicht sehr reproduzierbar und signifikant im Vergleich zur Untersuchung von reinen Polymeren.
Nach Abschluss eines Produktionszyklus kühlt die Form ab, und das Teil wird ausgeworfen.
Obwohl dieser Prozess erfolgreich ist, um akzeptable, gut funktionierende Teile herzustellen, bot sich eine Optimierungsmöglichkeit in den Zykluszeiten. In Anbetracht dessen begann NETZSCH Pumpen & Systeme ihre Zusammenarbeit mit sensXPERT im Jahr 2021.
Die Zusammenarbeit zwischen sensXPERT und NETZSCH Pumpen & Systeme
Mit dem Hauptziel, die Zykluszeiten zu verkürzen, wurde die Lösung sensXPERT Insight in den Produktionsprozess der Gummistator integriert. Neben der Reduzierung der Zykluszeiten bietet sensXPERT eine Lösung, die Einblicke in die Charakterisierung der In-Form-Materialdaten ermöglicht und Prozessergebnisse prognostiziert. Mit einer Kombination aus fortschrittlicher Messtechnik und Materialwissenschaft sowie künstlicher Intelligenz kann diese Lösung den Einfluss interner und externer Formbedingungen auf die endgültige Bauteilqualität und -leistung präzise vorhersagen.
Vier Komponenten – dielektrische Sensoren, sensXPERT Blue Box, sensXPERT Live und sensXPERT Hub – sind in die Produktionsprozesse integriert.
Mit Hilfe der dielektrischen Analyse messen und verfolgen die dielektrische Sensoren das Verhalten des In-Form-Materials. Von Duroplasten und Thermoplasten bis hin zu Elastomeren und faserverstärkten Polymeren können diese Sensoren eine breite Palette von Materialien messen. Alle Sensordaten werden an das sensXPERT Blue Box übertragen, das alle eingehenden Daten scannt, mit Hilfe von maschinellem Lernen Muster erkennt und Ergebnisse in jedem Prozess prognostiziert.
Die sensXPERT Live visualisiert die Daten und dient als Echtzeitüberwachungsanzeige für Prozessoperatoren. Schließlich sammelt der sensXPERT Hub alle historischen Prozessdaten und ist ein wichtiges digitales Werkzeug im sensXPERT-Paket. Mit Hilfe der Hub können Hersteller Daten über mehrere Produktionsstandorte hinweg vergleichen und so alle Optimierungsmöglichkeiten finden.
Für den Produktionsprozess wurden die Sensoreinsätze von sensXPERT gründlich geprüft und vor der Integration mit NETZSCH Pumpen & Systeme diskutiert.
Zunächst untersuchten Werkzeugexperten die Statorbauteile und wiesen auf die Stellen hin, an denen die Wanddicke am höchsten war. Das thermische Verhalten eines Abschnitts mit höherer Wanddicke ist komplexer als bei Abschnitten mit geringerer Wanddicke, was den ersteren zum geeignetsten Ort für die Positionierung eines Sensors und zur Messung macht.
Anschließend umfasste der Produktionsprozess, der im Mittelpunkt dieses Falles stand, die Instrumentierung jeder Formhöhle mit einem Materialcharakterisierungssensor. Aufgrund der Positionierung der Höhlen passte sensXPERT die Sensorkabel an, um eine ausreichende Reichweite zu gewährleisten.
“Wir erwarten, dass die neue Technologie die Effizienz durch signifikante Reduzierung der Zykluszeiten erheblich steigert. Wir freuen uns sehr, unser Unternehmensprojekt sensXPERT® durch diese Zusammenarbeit unterstützen zu können und Mehrwert für uns selbst zu generieren. Diese KI-basierte Technologie unterstützt perfekt unser Bestreben, unsere Wertschöpfungskette weiter zu automatisieren und zu digitalisieren.” Jens Heidkötter, Geschäftsführer bei NETZSCH Pumpen & Systeme
Messungen, Validierung & Ergebnisse
Schließlich konnten mit dem außerhalb, aber in der Nähe der Spritzgießmaschine platzierten Blue Box sensXPERT-Messungen durchgeführt werden.
Basierend auf den anfänglichen Daten, die über die Sensoren und das Blue Box gesammelt wurden, erstellten die Datenwissenschaftler von sensXPERT ein maschinelles Lernmodell. Mit dem ersten ML-Modell führten NETZSCH Pumpen & Systeme und die Datenwissenschaftler von sensXPERT eine Validierung des Modells vor Ort durch. Anweisungen wurden gegeben, um den Spritzgießzyklus manuell zu stoppen, sobald das Modell vorhersagte, dass ein bestimmter Grad der Vulkanisation erreicht war. Anschließend wurden Probemuster getestet, um die Vorhersagefähigkeiten des Modells zu validieren. Der Validierungsschritt ermöglichte die weitere Entwicklung des ML-Modells.
Nach der Validierung wurde ein Stoppauslöser in den Prozess eingeführt. Dies stellt sicher, dass, sobald ein Zyklus gemäß dem Vorhersagemodell den gewünschten Vulkanisationsgrad erreicht hat, das Blue Box einen Trigger sendet, um die Maschine und den Spritzgießzyklus automatisch anzuhalten.
Alles in allem führte die Zusammenarbeit zwischen sensXPERT und NETZSCH Pumpen & Systeme zu mehreren erfolgreichen Ergebnissen. Das folgende Histogramm veranschaulicht das potenzielle Zeitersparnispotenzial während der Vulkanisation. Das Histogramm zeigt, wie die Integration von sensXPERT im Durchschnitt ein Einsparpotenzial von 23 % der Vulkanisationszeit bietet, wobei die minimalen und maximalen potenziellen Einsparungen bei extremen Zyklen bei 14 % bzw. 32 % liegen.
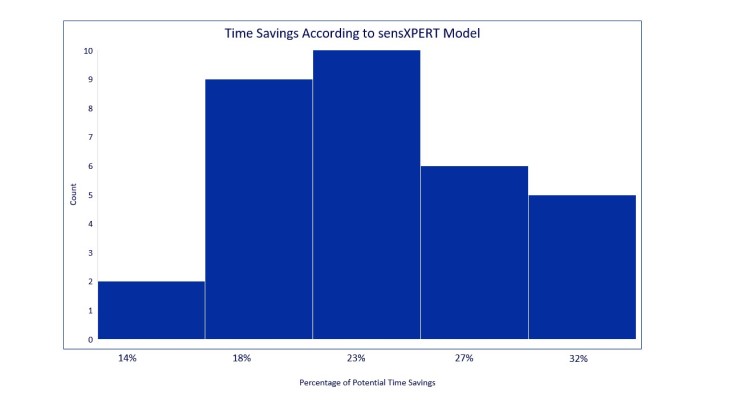
Die sensXPERT-Lösung soll NETZSCH Pumpen & Systeme voraussichtlich etwa 15 % der Produktionszykluszeit für ihre Gummistatorproduktion einsparen. Daher werden durch die kürzere Herstellungszeit dieser Teile zusätzliche Vorteile erzielt, wie geringere Energieausgaben und mehr Zeitersparnis für das Personal.
“Während der Aushärtezeit ist die Maschine geschlossen, und niemand weiß, was auf molekularer Ebene passiert. Daher ist der Prozess wie eine Black Box. Typischerweise wird eine feste Heizzeit für ein Teil festgelegt, um den geforderten Aushärtegrad zu erreichen, der dem Teil seine optimalen mechanischen Eigenschaften verleihen sollte. Es gibt jedoch verschiedene Einflüsse auf das Material, wie z.B. Variationen in den Chargen, Formtemperaturen und Umgebung. Um mit diesen Einflüssen umzugehen, wird die Heizzeit vorsorglich verlängert. Dies ist der sogenannte Angstfaktor. Mit Hilfe von sensXPERT® können wir nun sehen, was im Material passiert, wenn die Form geschlossen ist. Die Lösung misst den Aushärtegrad, sagt den Prozess anhand der gesammelten Daten voraus und stoppt die Heizung genau dann, wenn die optimalen mechanischen Eigenschaften erreicht sind. Somit ermöglicht uns sensXPERT®, komplexe Teile in höchster Qualität herzustellen und Maschinenzeit zu sparen, was zu niedrigeren Produktionskosten und höherer Produktivität führt. Deshalb freuen wir uns sehr, einer der ersten Partner in diesem Bereich zu sein.” Frank Götz, Prozessingenieur bei NETZSCH Pumpen & Systeme
Letztendlich erzielt sensXPERT Insight eine höhere Prozesseffizienz in zahlreichen Fertigungsumgebungen. Die Lösung kombiniert das leistungsstarke sensXPERT Blue Box – mit einer Stopptastenfunktion -, die dielektrische Sensoren und die Hub (Cloud-Zugänglichkeit), um Hersteller bei der Prozessautomatisierung, Transparenz und Digitalisierung zu unterstützen. Darüber hinaus können Hersteller – wie NETZSCH Pumpen & Systeme – einen digitalen Faden pro produziertem Teil erhalten, langfristige Trends und Drifts in den Daten beobachten und Optimierungsmöglichkeiten im Prozess durch den sensXPERT Hub identifizieren
Quellen:
[1] Creating value in flow control | McKinsey
[2] NEMO® Progressing Cavity Pumps – NETZSCH Pumpen & Systeme