Wie Sie die Herstellung von Verbundwerkstoffen in der Luft- und Raumfahrt optimieren
Im Jahr 2022 betrug die geschätzte Marktgöße der weltweiten Luftfahrtkunststoffindustrie 7,14 Milliarden US-Dollar. Darüber hinaus wird erwartet, dass die steigende Nachfrage nach verschiedenen in Verbundwerkstoffen hergestellten Luftfahrtstrukturen das anhaltende Wachstum der Branche vorantreiben wird. Die steigende Nachfrage nach der Produktion von Luftfahrtstrukturen ist auf das wachsende Bedürfnis der Verbraucher nach Luftreisen nach der COVID-19-Pandemie zurückzuführen. Darüber hinaus, wie im Folgenden näher erläutert wird, haben Luftfahrtunternehmen eine Phase der Produktionswiederherstellung und -optimierung erreicht.
Die Herstellung von Kunststoffen hat in vielen Branchen aufgrund der Vorteile, die diese Materialien mit sich bringen, Erfolg gefunden. Kunststoffe, insbesondere Kunststoffverbundwerkstoffe, sind im Vergleich zu traditionellen Materialien wie Aluminium und Stahl leichter und vielseitiger.
Im Verlauf dieses Artikels möchten wir verschiedene Verfahren zur Herstellung von Verbundstrukturen für Luftfahrtanwendungen erläutern, auf einige kürzlich von Luftfahrtunternehmen erlebte Schwierigkeiten eingehen und aufzeigen, wie Hersteller ihre Prozesse optimieren können, um die Effizienz und Produktivität zu steigern.
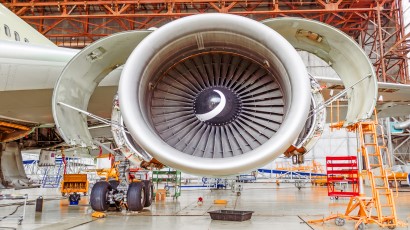
Beispiele für Fertigungsprozesse von Verbundwerkstoffen in der Luft- und Raumfahrt
Für Luft- und Raumfahrtanwendungen hergestellte Teile müssen in der Regel Eigenschaften wie ein hohes Festigkeits-Gewichts-Verhältnis und Korrosionsbeständigkeit aufweisen, um die anspruchsvollen Anforderungen der Luft- und Raumfahrtindustrie zu erfüllen, darunter Gewichts- und Kraftstoffeffizienz, strukturelle Integrität, Langlebigkeit und Sicherheit. In der Branche werden verschiedene Verfahren verwendet, um solche Teile herzustellen, ein Beispiel ist die Harzinjektion und die Aushärtung im Autoklav.
Harzinjektion und Aushärtung im Autoklav
Die Harzinfusion ist ein Herstellungsverfahren für Verbundwerkstoffe, bei dem trockene Faserverstärkungen wie Kohle- oder Glasfasern mit einem flüssigen Harz imprägniert werden, um leichte und langlebige Verbundwerkstoffe zu erzeugen.
Je nach den spezifischen Anforderungen und Anwendungen in der Luft- und Raumfahrt können unterschiedliche Fasern für die Harzinfusion ausgewählt werden. Kohlefaser wird in der Luft- und Raumfahrt aufgrund ihrer außergewöhnlichen Festigkeit und Leichtigkeit häufig verwendet. Darüber hinaus werden Epoxidharze aufgrund ihrer thermischen Stabilität, mechanischen Eigenschaften und ihrer hervorragenden Faser/Matrix-Bindung im Allgemeinen eingesetzt.
Der Harzinfusionsprozess beginnt mit der Anordnung der trockenen Fasern zu einem Preform. Diese Anordnung ist äußerst entscheidend, da sie die mechanischen Eigenschaften des endgültigen Verbundteils beeinflusst. Der nächste Schritt in diesem Prozess ist die sorgfältige Platzierung des trockenen Faser-Preforms in eine Form, die dann abgedichtet wird, um eine luftdichte Umgebung zu schaffen.
Ein flüssiges Harz wird dann durch ein Netzwerk von Rohren in die versiegelte Form geschickt. Um sicherzustellen, dass das Harz ausreichend durch die trockene Faserverstärkung fließt, wird ein Vakuum auf die Form aufgebracht, um das Harz zu verteilen und Luft zu entfernen. Nachdem das Harz in die Fasern eingedrungen ist, wird die gesamte Form in der Regel in einen Autoklaven platziert, um das Harz auszuhärten und den Verbundwerkstoff zu verfestigen.
Der Autoklav
Ein Autoklav ist eine verschlossene Kammer, in der der Inhalt unter kontrollierten Bedingungen hoher Temperatur und hohem Druck platziert wird, um Materialien, wie das zuvor erwähnte Harz, auszuhärten. Nach einem Aushärtezyklus kühlt der Autoklav langsam ab. Diese kontrollierte Abkühlphase wird durchgeführt, um thermische Spannungen zu verhindern und die strukturelle Integrität der Verbundbauteile zu erhalten.

Neue Prozessüberlegungen in der Luft- und Raumfahrtfertigung
Neben der Harzinjektion und dem Aushärten im Autoklav werden alternative Prozesse für die Herstellung von Verbundwerkstoffteilen in der Luft- und Raumfahrt in Betracht gezogen. Ein solcher Prozess ist das sogenannte Harztransferverfahren (RTM), das dem Harzeinflussverfahren sehr ähnlich ist, da bei beiden Prozessen trockene Faserverstärkungen mit Harz durchtränkt werden. Es gibt jedoch Unterschiede hinsichtlich des verwendeten Drucks, der Steuerung der Harzverteilung und der Anwendungen, für die sie am besten geeignet sind. Das Harzinjektionsverfahren wird häufig zur Herstellung von Teilen mit komplexen Formen verwendet, bei denen eine präzise Faserkontrolle von geringerer Bedeutung ist. RTM ist hingegen bevorzugt für höchste Präzision und gleichmäßige Harzverteilung und eignet sich daher besonders für die Herstellung von tragenden Bauteilen.
RTM ist ein geschlossener Flüssigkeitsverbundformprozess, bei dem Harz in eine Form mit vorgefertigten trockenen Verstärkungsmaterialien injiziert wird, um Verbundwerkstoffteile herzustellen. Der Prozess beginnt mit der Vorbereitung von zwei Formhälften, die die gewünschte Form und Abmessungen des endgültigen Verbundwerkstoffteils erzeugen sollen. Die trockenen Verstärkungsmaterialien werden präzise in einer der Formhälften platziert und strategisch geschichtet, um die gewünschten Festigkeits- und Leistungseigenschaften zu erreichen. Die beiden Formhälften werden dann sicher miteinander verschlossen, wodurch die trockenen Verstärkungsmaterialien im Formhohlraum eingeschlossen werden.
Ein flüssiges Harzsystem wird dann unter kontrolliertem Druck durch Leitungen und Tore in die Form injiziert. Das Harz durchtränkt die trockenen Verstärkungsmaterialien, um eine feste Verbundstruktur zu schaffen. Zur Aushärtung des Harzes wird Wärme auf den Forminhalt aufgebracht. Nach Abschluss des Aushärtezyklus und der Aushärtung des Verbundmaterials wird die Form geöffnet, und das endgültige Verbundteil wird aus der Form genommen.
Eine Phase der Schwierigkeiten und Instabilität
Die Verwendung von Kunststoffen anstelle von Metallen und Prozessentwicklungen wie die Einführung von RTM in der Luftfahrtindustrie deuten auf die Innovationsfähigkeit der Branche hin. Die Hersteller in der Luftfahrtindustrie haben die Grenzen der Flugzeugeffizienz erweitert, aber diese Fortschritte wurden auch durch Rückschläge begleitet. Zum Beispiel führte der Ausbruch der COVID-19-Pandemie zu einer Reihe von Schwierigkeiten, von denen die Branche immer noch betroffen ist.
Insgesamt beeinflusste die Pandemie vorübergehend einen erheblichen Rückgang der Nachfrage, Unterbrechungen in den Lieferketten, finanzielle Verluste und Beeinträchtigungen der Arbeitskräfte. Der Ausbruch der Pandemie führte zu einem plötzlichen und starken Rückgang des globalen Flugverkehrs. Als Folge von Lockdowns, Reisebeschränkungen und der Zurückhaltung der Passagiere, zu fliegen, reduzierten zahlreiche Fluggesellschaften ihre Flotten und stornierten Bestellungen für neue Flugzeuge. All dies führte zu einem Kaskadeneffekt in der Lieferkette der Luftfahrtindustrie, der Verzögerungen, Entlassungen und erhebliche Umsatzverluste für die Hersteller verursachte.
Wie von McKinsey & Company berichtet, hatten die Hersteller in der Luftfahrtbranche im Jahr 2020 Verluste in Höhe von 12 Milliarden US-Dollar zu verzeichnen. Angesichts der erheblichen finanziellen Nachteile der Fluggesellschaften wurden weniger neue Bestellungen aufgegeben und mehr Lieferungen ausgesetzt oder verschoben.
Dieser finanzielle Druck zwang die Hersteller, ihre Produktionspläne und die Zahl der Mitarbeiter neu zu bewerten. Die Ergebnisse waren erhebliche Entlassungen und freiwillige Pensionierungen, und viele kleinere Hersteller arbeiteten mit erheblich reduzierter Kapazität oder standen vor vorübergehenden Schließungen. Dies führte zu erheblichen Unterbrechungen der globalen Lieferketten und Verzögerungen bei der Lieferung wichtiger Komponenten und Materialien an die Hersteller in der Luftfahrtindustrie. Dies verschärfte die Produktionsherausforderungen weiter.
Nach der Lockerung der COVID-19-Lockdowns und -beschränkungen begann die Nachfrage nach Flugreisen wieder anzusteigen. Entsprechend nahmen die Fluggesellschaften Bestellungen für neue Flugzeuge wieder auf und die Produktionsraten stiegen an, was die Hersteller dazu veranlasste, die Produktionsprozesse zu optimieren, um auf diesen Anstieg der Bestellungen vorbereitet zu sein.

Wie Sie die Herstellung von Luft- und Raumfahrtverbundwerkstoffen optimieren, um die Produktivität und Effizienz zu steigern
Der Beginn von Industrie 4.0 hat die Entwicklung und Verbesserung von Technologien angeregt, die darauf abzielen, die Prozesseffizienz und Produktivität zu steigern. Von Robotik und Automatisierung bis hin zu künstlicher Intelligenz und Cloud-Computing haben Hersteller nun Zugang zu einer Fülle von Innovationen, um ihre Prozesse zu optimieren.
Eine solche Innovation ist sensXPERT Digital Mold mit seiner Kombination aus Materialcharakterisierungssensoren, maschinellem Lernen und Cloud-Computing-Technologie, um Kunststoff- und Verbundwerkstoffherstellungsprozesse in Echtzeit zu überwachen, vorherzusagen und zu optimieren. Das Zusammenführen von Hardware, Software und Datenanalytik hat eine Lösung hervorgebracht, die es Herstellern ermöglicht, lebenswichtige Prozessparameter in Echtzeit zu verfolgen, wie beispielsweise den Vernetzungsgrad, die Glasübergangstemperatur, die Viskosität und die Fließfront.
Darüber hinaus werden alle gesammelten Prozessdaten verwendet, um maschinelles Lernen und Vorhersagemodelle zu trainieren, die Prozessergebnisse vorhersagen und das Ende eines Prozesses auslösen, sobald bestimmte Qualitätskriterien erfüllt sind. Neben dem Vorteil, stets die gewünschten Parameter zu erreichen, erzielt sensXPERT Digital Mold eine Reduzierung von bis zu 50% bei vorhandenem Ausschuss, eine Steigerung von bis zu 23% bei Energieeinsparungen und eine Verringerung der Zykluszeit um bis zu 30%. Insgesamt ermöglicht diese Lösung eine Echtzeit-Prozesskontrolle, um sicherzustellen, dass die Prozesse effizient und produktiv bleiben.
Durch die Integration von sensXPERT Digital Mold in die Herstellungsprozesse von Verbundwerkstoffen in der Luft- und Raumfahrt gewinnen Hersteller einen digitalen Faden pro produziertem Teil, benötigen weniger manuelle Arbeit, erhöhen die Qualitätskontrolle und erreichen eine dynamische Prozessanpassung. Ihre Prozesse sind daher besser gerüstet, um die steigende Anzahl von Aufträgen für Luft- und Raumfahrtstrukturen zu bewältigen.
Wenn Sie mehr über die Vorteile von sensXPERT Digital Mold für die Luftfahrtindustrie erfahren möchten, können Sie unsere Erfolgsgeschichte zur „Digitalisierung der Herstellung von Verbundwerkstoffen in der Luftfahrtindustrie“ lesen.