Exploring the Plastic Industry’s Materials Landscape
To be well-informed in plastics manufacturing environments, considerable understanding of the materials involved is paramount. Found in daily consumer products and components used in significant industries such as automotive, aviation, and electronics, plastic use is widespread. So, what makes plastic so versatile and functional? The answer can be found in the careful selection and application of the materials that compose plastic parts.

In this blog article, we will explore the material landscape in plastics manufacturing. First, we will present the history of plastic. Subsequently, we will reveal various types of plastic material, their advantages, and their applications. Finally, we will highlight a few factors that are considered when a certain material is selected in manufacturing.
By the end of this article, you will have gained a comprehensive understanding of the plastics manufacturing materials landscape and how it shapes the products we encounter daily.
What is Plastic?
Plastics are synthetic or semi-synthetic substances that are primarily composed of polymers. A polymer is a large molecule made up of smaller repeating subunits, or monomers. Plastics are derived from petrochemicals or renewable resources, and they can present a range of properties and characteristics, including the following:
- Lightweight
- Durability
- Elasticity
- Chemical resistance
- Electrical insulation
- Transparency
Under certain conditions, such as temperature and pressure, plastic materials can be molded into various shapes and sizes in manufacturing environments. Its versatility makes the material incredibly desirable for many applications in different industries.
The History of Plastic
Since its discovery, the development and production of plastic has witnessed many significant breakthroughs. The name itself stems from the material’s pliable and easily shapeable traits, making it desirable for a myriad of industries. The timeline below illustrates a few considerable developments throughout the history of plastic.
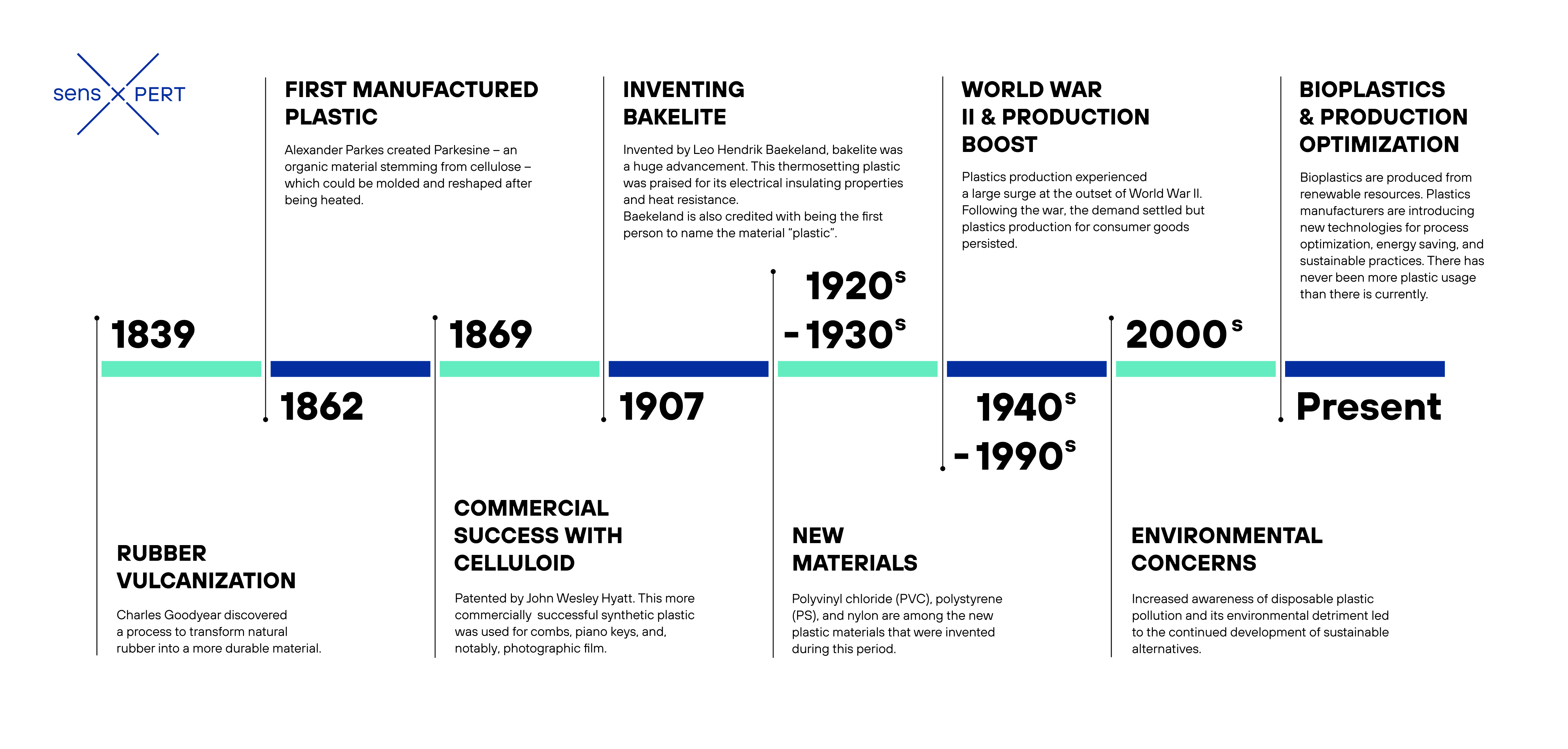
Different Types of Plastic: Advantages and Applications
Plastic materials encompass a vast array of polymers, each with their individual properties, applications, and advantages. Plastics can be assigned to various categories or classifications, with thermoplastics, thermosets, elastomers, and composites being among the most common.
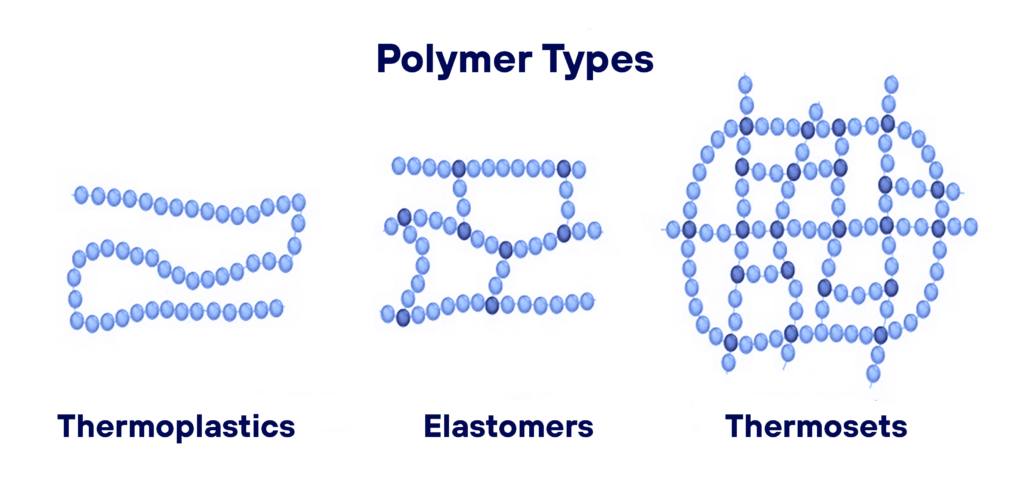
Thermoplastics
Due to their molecular properties, thermoplastics can be melted and re-molded several times. At room temperature, these products are solid. However, once heat is applied to them, they soften and become fluid. Due to the lack of chemical bonds formed between the polymer molecules during processing, these materials can be recycled, reheated, and remolded multiple times. Generally, plastics within this category have low melting points, making them suitable for applications using recycled materials. Three examples of thermoplastics are:
- Polyethylene (PE): This versatile thermoplastic is well-known for its chemical resistance, availability, and flexibility. It is commonly used in packaging materials, plastic bags, containers, pipes, and automotive components.
- Polypropylene (PP): With high strength, stiffness, and heat and chemical resistance, polypropylene is often used in packaging, appliances, medical devices, and textiles.
- Polyamid (PA6, Nylon): This silk-like, synthetic material is commercially used to make clothing, such as raincoats and swimwear. The material’s industrial applications include conveyer and seat belts, nets, parachutes, and more. Polyamid is known for its strength, durability, and abrasion resistance. It is also better suited for high temperatures and mechanical requirements.
Thermosetting Plastics
Otherwise called thermosets, these plastics are unlike thermoplastics in that they form chemical cross-links between their molecules when cured. Additionally, once this material is heated, or cured, the reaction is irreversible. Their properties permanently change, and the thermosets can no longer be softened or reshaped. Common applications for thermosets are in the automotive, aviation, and electrical encapsulation industries. Examples of thermosets include epoxy resins, phenolics, and bismaleimide (BMI).
- Epoxy resins: With excellent adhesion, chemical resistance, and mechanical properties, epoxy resins are best suited for coatings, adhesives, and structural components.
- Phenolics: Phenolic plastics are heat resistant, offer electrical insulation, and have dimensional stability. They are generally used in electrical and insulation applications.
- Bismaleimide (BMI): BMI resins possess high heat resistance, which makes them ideal for aerospace applications including aircraft components and high temperature adhesives.
Elastomers
These polymers are best recognized by their elastic properties, which enables them to stretch and return to their original shape. Elastomers have applications in industries like healthcare, consumer goods, and automotive. Resilience and flexibility make elastomers ideal for the production of tires, footwear, sealing, among others.
Composites
Composites are composed of two or more various types of materials. For example, the combination of plastics with reinforcing fibers, such as fiberglass or carbon fiber allows composites to offer strength, stiffness, and lightweight properties in comparison to more traditional materials. Composite use can be found in the aviation, automotive, construction, and sporting goods industries.
Considerations and Selection in Plastics Manufacturing
Material expertise empowers manufacturers in the plastics industry to select the most appropriate materials for specific applications. Factors like mechanical properties, chemical compatibility, temperature resistance, and manufacturing processes undergo careful consideration to ensure the desired performance and functionality of the final plastic part.
Mechanical Properties
Mechanical properties of plastics include tensile strength, flexibility, impact resistance, and hardness. Some applications might require materials that can withstand forces, vibrations, or other stresses.
Chemical Compatibility
During use, plastic products might encounter various chemical and atmospheric stress, making it essential to assess a material’s chemical compatibility to ensure corrosion or degradation resistance.
Temperature Resistance
Plastic products can have applications in industries that encounter extreme temperatures; aviation to name an example. To avoid deformation or performance issues, understanding a material’s temperature resistance is critical.
Manufacturing Process
The selected material must be compatible with a specific manufacturing process. Each process, from injection molding to extrusion, has certain requirements regarding viscosity, cooling, melt flow, and more. Successful manufacturing relies on material understanding.
By carefully considering the outlined factors and building strong material knowledge, manufacturers can guarantee the alignment of their processes with their chosen materials, which also enhances process stability, final part quality, and cost/energy efficiency.