Demystifying sensXPERT
We have a lot to unpack. We have told you a lot so far, but now we want to share how sensXPERT technology really works. Hence, we are now on a mission: Demystifying sensXPERT.
We’d like to get straight to the point by clearing up a misunderstanding. sensXPERT is our brand. Our company name is NETZSCH Process Intelligence GmbH. We belong to the NETZSCH group, which transforms industries with next-level intelligence for increased efficiency, quality assurance, and process reliability for the plastics industry. NETZSCH Process Intelligence GmbH is the first NETZSCH corporate venture, with a mission of enhancing productivity through advanced process analytical technology for industry 4.0. In a nutshell, we take your process and material data and turn them into a powerful dynamic duo, creating a performance and real-time quality-controlled manufacturing landscape. To do so, our in-mold sensors measure and characterize varying material parameters and feed them into the sensXPERT Blue Box. The high-power IPC provides real-time process answers, identifying material and process deviations immediately.
We install…in-mold dielectric sensors
Manufactured in-house and with over 20 years of sensor know-how, the in-mold dielectric sensors deliver valuable material data and process information that traditional temperature and pressure sensors cannot provide. While the Blue Box evaluates the sensor information and gives process suggestions in real time, all necessary data is displayed on sensXPERT Live for maximum process control and transparency.
But that is not where our sensXPERT technology stops. We want processed data that adds value and is not only stored in the sensXPERT Hub. In this case, we combine our extensive material knowledge and technological possibilities. sensXPERT builds machine learning models in no time using kinetic models, historical client data, and real-time production data. With these models, we can predict the optimum point of cure/crystallization while your production is running, allowing for digital component tracking and quality control on each part produced. Continuous retraining of the machine learning models happens in the Hub, where all historical production and third-party data are collected and visualized.
This is one of the mysteries we demystify in this blog post. How does the logic behind sensXPERT’s dielectric analysis work? We make something previously invisible visible and predict errors before they occur. Dielectric analysis works by measuring material behavior under an applied electric field. The measurement technology differs from other dielectric technologies, using interdigitated or comb configurations to enable a single flat measurement surface to be directly installed into any mold.
An electric field across the dielectric sensor causes ion motion and dipole rotation in the material. Positively charged ions move toward the negatively charged electrode, and negatively charged ions are attracted to the positively charged electrode. As the material cures or solidifies, the flow of the ions is restricted, resulting in decreased conductivity. This translates to an increase in the mechanical viscosity of the material.
As such, the sensXPERT sensors measure various material properties, like ion viscosity or temperature, and determine the degree of cure and the glass transition temperature in a kinetic model.
We offer… Equipment-as-a-Service
You might wonder, “What do you actually do?”. The quick answer is that sensXPERT is an Equipment-as-a-Service product. Carefree hardware for lease that includes support for manufacturing optimization using the latest AI and cloud technology. The multi-level offer includes
- in-house manufactured in-mold DEA sensors to measure and calculate diverse material parameters;
- the sensXPERT Blue Box to evaluate machine and material data for automated data analytics to optimize your part production and increase overall equipment efficiency in real-time, thus allowing for traceable, sustainable manufacturing;
- sensXPERT Live, an interface to the Blue Box, that delivers real-time predictions on the running part processing and displays material behavior. It notifies the controller on how to adapt the process for optimal efficiency;
- sensXPERT Hub, a cloud service that allows you to create customizable dashboards and track trends using the parameters most important to you; and
- a monthly subscription model with low initial setup costs.
We measure and calculate… detailed data on every part produced
The data we measure, see, and evaluate propels the change towards dynamic and driven manufacturing. In a nutshell, we rely on sufficient material property measurements focusing on resin and ion viscosity and material conditions like mixing ratio, aging, shrinkage, and contamination.
The information inflow from your daily produced parts and process data, such as cycle times, allow us to predict the exact degree of cure/crystallization (DoC) and glass-transition temperature. The molder specifies the target DoC value, and our system can send an alert once it is achieved.
It is not just the material properties that matter for high-standard process control. sensXPERT is an intelligent system that processes information. It combines data from machines, peripheral equipment, and third-party sensors to provide maximum transparency and ensure an overall productivity increase.
The processing landscape is vast, and so is the variety we support:
- Reaction Injection Molding
- Thermoforming & Compression Molding
- Transfer Molding Processes
- Vacuum Infusion & Autoclave Curing
sensXPERT measures thermosets, thermoplastics, and elastomers and is also able to work with material combinations and mixes that use reinforcement, composite or filler materials. This is crucial in processing recycled materials and achieving a circular plastics economy.
We’ll give you an example
Let’s look at a carbon fiber epoxy prepreg example. Today’s conventional in-mold technologies measure pressure and monitor temperature and time. Is that enough? We can clearly say…no! In our analysis of carbon fiber epoxy prepregs, the material cures and solidifies during different temperature steps, but the progression of real-time curing still needs to be included. Eventually, the part gets de-molded, but what if the part lacks sufficient curing and the mechanical properties have not adequately developed, often leading to part deformation and scrap?
What is the alternative to this process? Let’s get to the bottom of sensXPERT’s technology. The dielectric sensors detect material parameters critical for the process based on the microscopic polymer behavior and deviations. The result is an exact calculation and display of the degree of cure or crystallization, allowing for a dynamically controlled process. Instead of relying on pre-defined material data sheets or assumptions, the molder is now the master of the curing process and production dynamics.
We are more than measurements… machine learning models predict process parameters
First, we use sensor data to create a kinetic model, which can predict the degree of cure/crystallization, glass transition temperature, or other relevant thermal and mechanical properties of your material. Once this kinetic model is created, shop floor data from your running production is collected, and all the data is used to build a powerful machine learning model. With that machine learning model, we can precisely predict process information and enable you to dynamically control the process to ensure consistent part quality.
Then, the sensXPERT technology goes another step further. We also implement information from third-party sensors, including mold temperature, pressure transducers, ambient temperature, humidity, and anything else you would like to observe. sensXPERT’s machine learning models, specifically tailored to your needs, will then determine the most relevant information for the manufacturing process.
This is the precise point at which the production process reaches an unprecedented level. In the sensXPERT Hub, you can see the real-time status and predictions of material and products. Now, your dynamically controlled manufacturing reaches previously unattained quality levels and optimizes processes to the maximum, streamlining them to achieve optimal sustainable output.
We optimize… measurable data, driving maximum output
A core question is what does predictive analytics mean in everyday part production? It means measurable data, driving maximum output. sensXPERT’s artificial intelligence (AI)-based models calculate and predict material behavior better and faster than usual.
In a nutshell:
- In-mold sensors collect real-time production data (light blue dashed line).
- Combining collected machine, cavity, and material data lets the #machinelearning models do their magic to create reliable, trustworthy predictions (green dashed line).
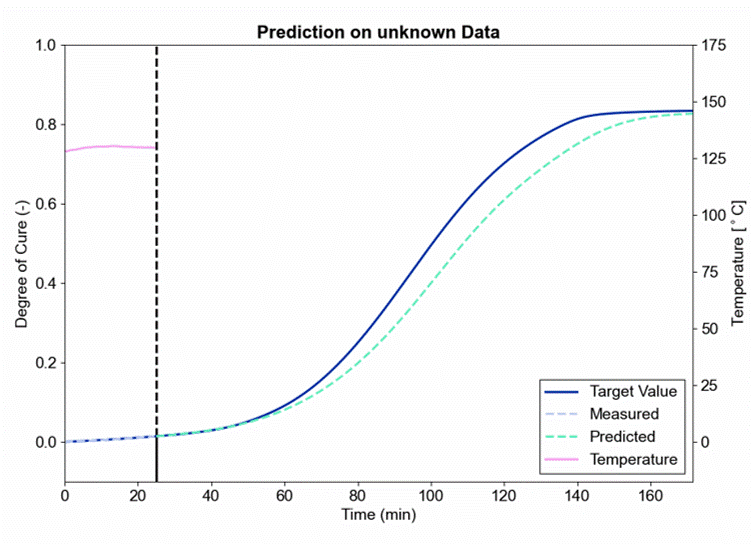
The predicted process can be dynamically adjusted if the processing part does not match the target value (solid blue line). In the visualized case, the curing cycle allows for increased exposure to a predetermined temperature (pink line) to reach the target degree of cure. The sensXPERT process control system can be monitored to ensure that parts are being optimally cured. If the process is not on track, operators can adaptively control the process to ensure desirable outcomes.
There is a crucial question to ask now… Artificial intelligence, production data in a cloud, software that supports machine operators to control processes – is that secure? Does a traditional and successful plastics production company even want that?
The sensXPERT Hub stores all necessary production data and calculations securely. From there, processors create a customized dashboard and observe process trends by serial numbers, operators, machines, or whatever else is important to them. The data is fully accessible to them – and only to them – and was built with Open API to easily connect to other systems and transfer if needed.
7 mysteries about sensXPERT unpacked
- We want processed data that adds value and is not just stored on the Cloud.
- We make previously invisible material behavior visible and predict errors before they occur.
- We offer an Equipment-as-a-Service product… carefree hardware for lease with a manufacturing process control solution.
- We measure and calculate detailed data on every part produced.
- We make molders the master of the curing process and production dynamics.
- We are more than measurements. Dynamically controlled manufacturing reaches permanently unattained quality levels.
- We ensure your data is securely stored and fully accessible only to you.