How Modern Manufacturers are Rethinking Elastomer Processing
Why real-time control is replacing guesswork, one part at a time.
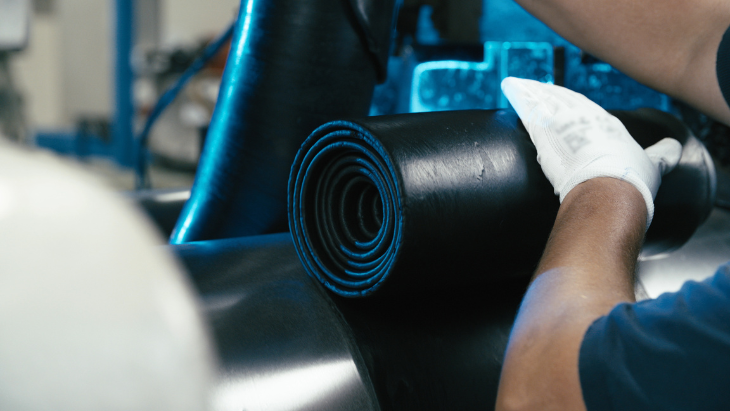
No two elastomers cure alike.
Elastomer parts can look identical to the naked eye, yet perform dramatically differently under stress, temperature, or time. That’s the reality many manufacturers face in elastomer component production: the unpredictable behavior of a class of materials known for their flexibility, but not necessarily their consistency.
As product specifications grow more demanding and tolerances tighten, manufacturers are beginning to realize that fixed cure times – often reflecting ideal processing conditions – rarely align with the real-world factory floor. Variations in batches, ambient conditions, and mold behavior can introduce blind spots that jeopardize part quality long before the stopwatch starts. What’s truly on the line? Mechanical integrity, long-term durability, and reliable performance of every part that leaves the mold.
This article explores the complexity of elastomer manufacturing, highlighting real production challenges and smarter strategies for overcoming them – far beyond conventional quality control. From understanding what makes each elastomer component unique to predicting part performance during the vulcanization process, we explore how manufacturers are stepping into a new era of data-driven control.
What are Elastomers?
Elastomers are a class of polymers known for their high elasticity. Their long-chain molecular structure enables them to stretch significantly and return to their original form. This flexibility, combined with an ability to withstand fluctuating temperatures, as well as chemical, UV light, and ozone exposure, makes them indispensable across industries – from automotive to aerospace and more.
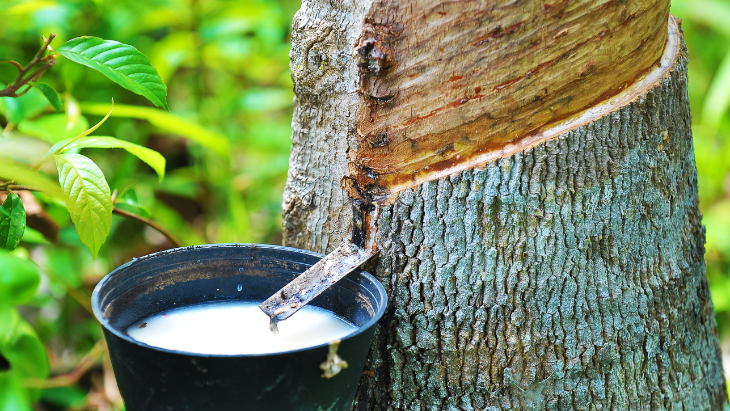
Elastomers can be broadly categorized into three groups:
- Natural Rubber: Sourced from rubber trees and processed into usable compounds.
- Synthetic Rubber: Produced from fossil-based monomers, with performance fine-tuned using fillers and additives.
- Silicone Rubber: Made from quartz sand, known for instance for their excellent heat resistance and flexibility.

Elastomers are commonly used to manufacture:
- Seals and gaskets
- Hoses and tubing
- Electrical insulators
- Vibration dampers
- Tires and footwear
Despite the shared “rubber” label, elastomers vary widely in both composition and behavior.
What Makes an Elastomer?
Elasticity: Can stretch up to several times their length and still return to form.
Resilience: Recover shape after deformation.
Cross-linking: Vulcanization introduces bonds that make the material durable.
Diversity: Includes NBR, EPDM, silicone, FKM, and others – each with unique vulcanization behaviors and properties.
Understanding Elastomer Types and Performance Tiers
The term “rubber” is often used interchangeably with elastomer, but there’s a key difference. Elastomer is a technical term referring to the broad class of elastic polymers. Rubber usually refers to a subset of elastomers, typically solid rubber compounds which include natural rubber, synthetic rubber and solid silicone types.
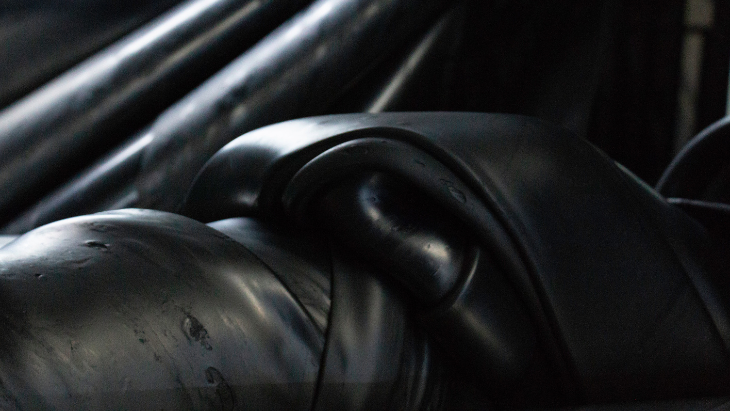
Even within a single elastomer type, like EPDM, formulations vary. One grade may vulcanize quickly at 160°C while another may need longer dwell times due to fillers or oil content. Often, the exact formulation of the compound is adjusted to the specific requirements of the application, resulting in a huge variety of compounds.
And here lies a major issue: Fixed cycle times fail to account for material-to-material variations.
Performance vs. Price in Elastomers
Commodity Elastomers (approx. 1–6 €/kg): NR, BR, SBR – used in tires, footwear, latex goods.
Engineering Elastomers (approx. 5–15 €/kg): EPDM, NBR, CR – used in gaskets, valves, dampers.
High-Performance Elastomers (approx. 15–400 €/kg): FKM, VMQ, FFKM – used in extreme environments, high media resistance, and applications requiring long lifetimes.
–
As performance and cost increase, so does the need for a more precise process and quality control
Common Elastomer Manufacturing Processes
Transforming raw compounds into functional components involves a variety of forming and curing techniques:
- Compression Molding: Widely used technique, especially for larger products or stamped parts.
- Injection Molding: High-speed production.
- Transfer Molding: Good control.
- Extrusion: Ideal for continuous profiles.
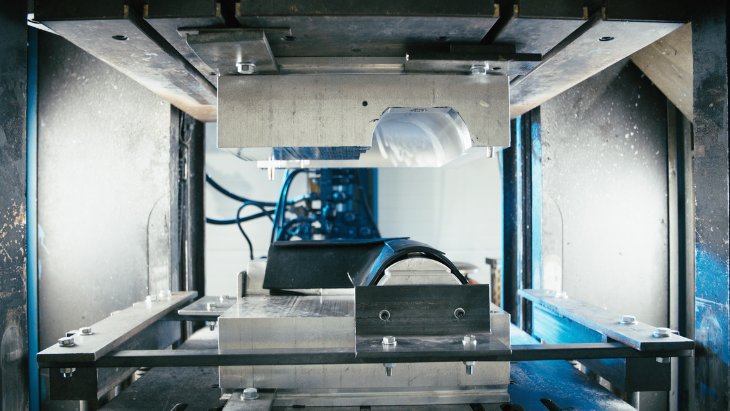
Each process introduces its own variables. But the biggest unknown across them all? Cure dynamics.
The Hidden Risks of Overcuring
Manufacturers often err on the side of caution, extending cure times to avoid under curing. However, this safety margin can backfire. Overcuring leads to degraded mechanical properties, brittle parts, increased scrap, and lengthened cycles – all without guaranteeing quality.
Even worse, these defects often go unnoticed until the final stages, sometimes only emerging during post-process quality assurance tests or long after the part has left the factory floor.
From Missed Defects to Measurable Performance
These late-stage issues highlight a deeper concern. Traditional quality control methods – centered on metrics like shore hardness or tensile strength – often overlook what truly matters: functional predictability.
- Will the part pass a discharge test?
- Will it adhere properly to a conductor or housing?
- Will it survive thermal cycling over time?
These questions demand more than static testing. Manufacturers need insight into what’s happening inside the mold, in real time.
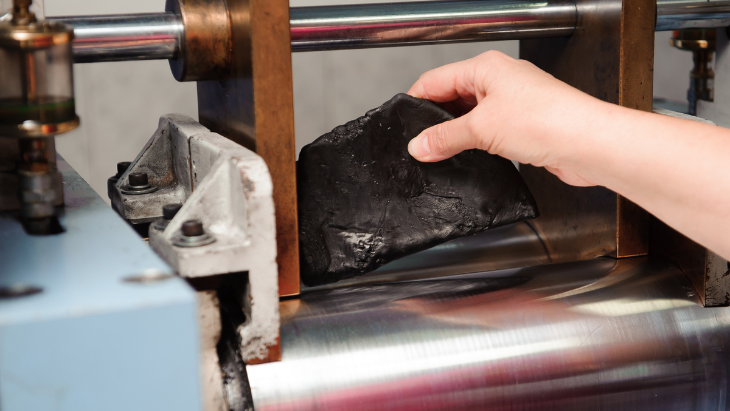
The Challenge: Complex Materials, Hidden Behavior
Despite advancements in machinery, much of the elastomer component production in the world remains highly manual. From the initial compound mixing and pressing through heated rolls, to manually cutting and loading preforms into molds, variability enters the process at nearly every step.
External influences such as room temperature, humidity, and even how long the mold is open before pressing can significantly affect results.
On top of that, many production facilities still rely on aging equipment and operator experience rather than digitized systems. The result? A persistent black box in the middle of the production process. Material behavior during vulcanization remains largely invisible.
Across all types, one thing is clear: no two elastomers cure alike. That’s why batch certificates and material spec sheets alone do not cut it. Even small formulation differences can lead to big deviations in vulcanization behavior and part performance.
Why Guesswork Still Dominates Rubber Component Production
–
- Most rubber part production lines still involve significant manual labor.
- Variations in material mixing, operator actions, and external conditions introduce unpredictable outcomes.
- Many elastomer molding machines are decades old and lack digital monitoring.
- Quality testing often occurs only after molding, leading to late-stage surprises.
–
These challenges make elastomer part production more difficult to control.
Real-Time Process Control: A Smarter Way to Cure
Enter sensXPERT.
Our solution brings real-time transparency to elastomer manufacturing. Using dielectric sensor technology embedded inside the mold, we monitor the material’s molecular response – measuring parameters such as ion mobility – to determine degree of vulcanization, cure kinetics, and material behavior.
We visualize cure progress, detect deviations, and predict outcomes while the part is still forming.
This allows manufacturers to end their cycles exactly when the material reaches optimal properties. The result? Better parts, less scrap, and shorter cycle times.
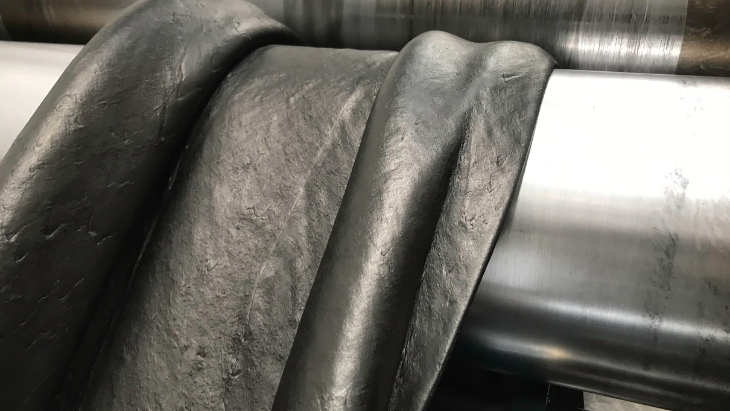
Proven Results: 15% Faster, 100% Smarter
Our collaboration with NETZSCH Pumps & Systems demonstrated the real-world value of smarter elastomer processing. By integrating sensXPERT Insight into their rubber stator production, they:
- Reduced cycle times by 15%
- Gained full visibility into in-mold material behavior
- Increased production efficiency
Read the full case study and see the results firsthand.
Join the Future of Elastomer Manufacturing
The need for modernization has never been more urgent. As labor costs rise and global competitiveness sharpens, many manufacturers are struggling to maintain margins, especially when production remains heavily manual. Even regions once known for low-cost production now face margin pressures.
Within this cost-sensitive manufacturing environment, reducing scrap, shortening cycle times, and avoiding post-production failures are critical to staying competitive and maintaining profitability.
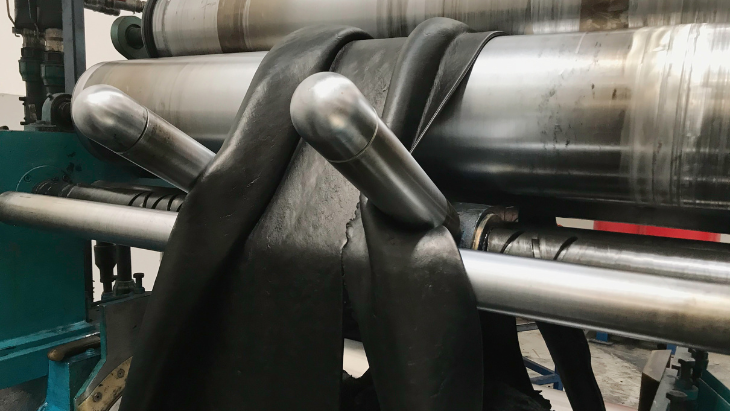
We’re just getting started. Whether you work with NBR, EPDM, silicone, or something else, sensXPERT adapts to your material and process realities.
Still relying on fixed cure times and static tests? Let’s change that.
Subscribe to our newsletter and keep an eye out for our upcoming webinar on elastomer manufacturing.
The future of elastomer manufacturing isn’t reactive — it’s predictive. Let’s rethink it, one part at a time.