Die Auswirkungen von Verbundwerkstoffen in der Luftfahrtindustrie
Die Luftfahrtindustrie hat eine Fülle von Fortschritten und Veränderungen erlebt. Materialien und Prozesse haben sich seit der Entwicklung des ersten motorisierten Fluges durch die Wright-Brüder im Jahr 1915 ständig weiterentwickelt, als dieser aus Drähten, Leinwand, Holz und Stahl gefertigt wurde. In den 1920er und 1930er Jahren erfolgte ein Übergang zu Metallen wie Aluminium, der als Metamorphose in Richtung leichter und langlebiger Flugzeugfertigung angesehen wurde.
Die Nachkriegszeit brachte noch weitere Fortschritte bei den Materialien mit der Einführung von Titan, einem Material, das gegen Ermüdung, Korrosion und hohe Temperaturen resistent ist. Allerdings stellte sich Titan schnell als sehr teuer und begrenzt in der Verfügbarkeit heraus.
Erstmals in den 1940er Jahren eingesetzt, war „[g]lasfaserverstärkter Kunststoff [GFK] oder Glasfaser das erste leichte Verbundwerkstoffmaterial, das in Flugzeugen eingesetzt wurde“ (Airbus). Eine Weiterentwicklung hin zu Kohlefaser kennzeichnete die Materiallandschaft der 1970er bis 1980er Jahre, und heute sind kohlefaserverstärkte Verbundwerkstoffe (CFK) besonders aufgrund ihrer Leichtbauweise zum Standard in der Luftfahrtfertigung geworden.
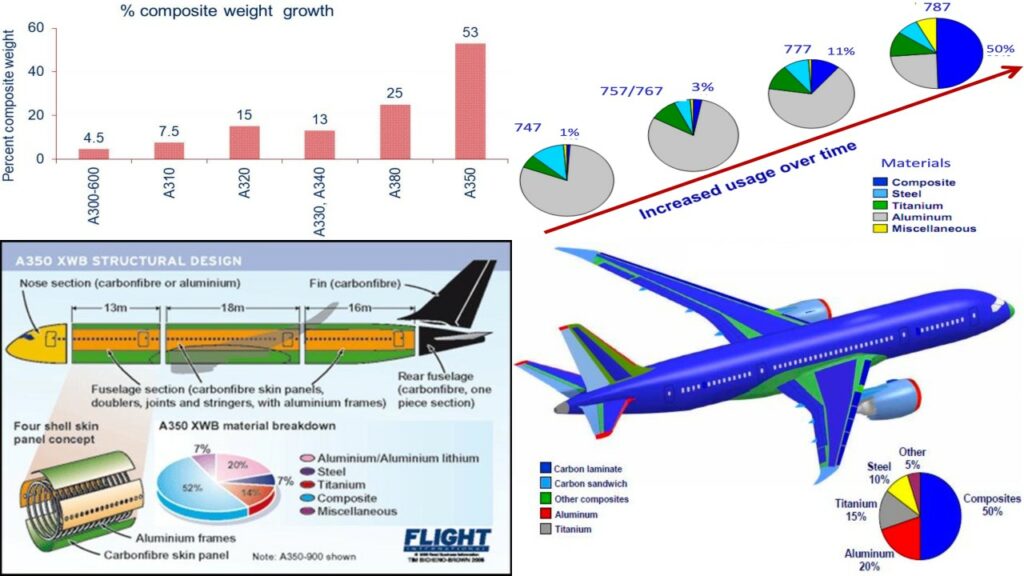
Der Einsatz von Verbundwerkstoffen bei Airbus und Boeing (Quelle: Flight International; Billy Roesler, et al., 100 Jahre Verbundwerkstoffe, ICCM16-2007; Douglas N. Ball, IDC HPC User Forum, Stuttgart, Deutschland; und Imperial College London, UK, Oktober 2008)
Auch die Herstellungsprozesse in der Luftfahrtindustrie haben eine lange Geschichte technologischer Fortschritte. Während des Ersten Weltkriegs, einer Zeit des Einsatzes von Holz und Leinwand, wurden Teile von geschickten Holzarbeitern und erfahrenen Näherinnen von Hand hergestellt, wie beispielsweise Holzrahmen und Hüllen für Flügel und Rümpfe.
Mit der Verwendung von Metallen wurden die Prozesse entsprechend angepasst. Dazu gehörten das manuelle Schneiden, Formen, Biegen und Umformen von Metallen sowie die Anwendung von Verfahren wie Schweißen und Flush-Nieten.

Die Verwendung von Metall im Flugzeugbau. Quelle: AIP Precision Machining
Mit dem Aufkommen von Verbundwerkstoffen wurden die traditionellen Metallbearbeitungsmaschinen von anderen Maschinen überholt, z.B. dem Autoklav, der im Blogartikel Wie Sie die Herstellung von Verbundwerkstoffen in der Luft- und Raumfahrt optimieren näher erläutert wird. In diesem Artikel erforschen wir, warum Kunststoffe und Verbundwerkstoffe in der Luftfahrtfertigung verwendet werden, welche Vorteile sie bieten und welche jüngsten Materialinnovationen den Einsatz von Kunststoffen in der Luftfahrt verbessern.

Die Vorteile von Kunststoffen und Verbundwerkstoffen in der Luftfahrtfertigung
Es herrscht allgemeine Übereinstimmung darüber, dass Flugzeuge extremen Temperaturen, Drücken und Belastungen ausgesetzt sind. Entsprechend wurden Kunststoffe und Verbundwerkstoffe aufgrund ihrer Fähigkeit, solche Hochleistungsanwendungen zu bewältigen, verstärkt eingesetzt.
Es gibt viele Gründe für den Einsatz von Kunststoffen und Verbundwerkstoffen in der Luftfahrtstrukturen. Dazu gehören Gewichtsreduzierung, Haltbarkeit, Designfaktoren, geringerer Wartungsaufwand, Lärmminderung, verbesserte Kraftstoffeffizienz und Korrosionsbeständigkeit.
- Gewichtsreduktion und verbesserte Kraftstoffeffizienz: Als einer der kritischsten Faktoren in der Luftfahrt tragen Kunststoffe und Verbundwerkstoffe zur Gewichtsreduzierung bei und sind leichter als herkömmliche Materialien wie Metall. Durch die Verringerung des Gesamtgewichts eines Flugzeugs wird die Kraftstoffeffizienz erhöht.
- Umweltaspekte: Entsprechend der Verbesserung der Kraftstoffeffizienz durch Kunststoffe und Verbundwerkstoffe tragen sie zur Verringerung der Umweltauswirkungen der Luftfahrt bei, indem sie zur Reduzierung von Emissionen beitragen.
- Haltbarkeit und Festigkeit: Trotz ihres geringen Gewichts bieten viele Kunststoffe und Verbundwerkstoffe ein hohes Festigkeits-Gewichts-Verhältnis, was sie ideal für Strukturkomponenten und Flugzeugteile macht, die hohen Belastungen standhalten müssen. Darüber hinaus sind diese Materialien korrosionsbeständig.
- Designfaktoren: Diese Materialien können in komplexe Formen mit unterschiedlichen Geometrien geformt werden. Diese Flexibilität ermöglicht es Ingenieuren, aerodynamische und effiziente Flugzeugformen zu gestalten.
- Wartungsreduktion: Gut ausgewählte Kunststoffe und Verbundwerkstoffe sind resistent gegen Umwelteinflüsse, wie Feuchtigkeit und Chemikalien, was den Bedarf an häufiger Wartung verringert. Dies führt auch zu niedrigeren Wartungskosten und weniger Ausfallzeiten der Flugzeuge.
- Lärmminderung: Einige Verbundwerkstoffe haben schalldämpfende Eigenschaften, die dazu beitragen können, den von Flugzeugen erzeugten Lärm zu reduzieren. Dies ist besonders wichtig für den Passagierkomfort und die Vorschriften zur Lärmbekämpfung.
- Korrosionsbeständigkeit: Im Gegensatz zu Metallen sind Kunststoffe und Verbundwerkstoffe, die in der Luftfahrt eingesetzt werden, korrosionsbeständig, was besonders für Flugzeuge, die in rauen Umgebungen oder über Salzwasserflächen operieren, von Bedeutung ist.
Mit dieser Liste von Vorteilen wurden Kunststoffe und Verbundwerkstoffe in verschiedenen Anwendungen in der Luftfahrt eingesetzt, einschließlich:
- Luftkanäle und Dichtungen für die Belüftung
- Flugzeugtüren, externe Verkleidungen und strukturelle Verstärkungen
- Innenwandverkleidungen und Gepäckfachablagen
- Interne Verkabelung, Buchsen und Lager
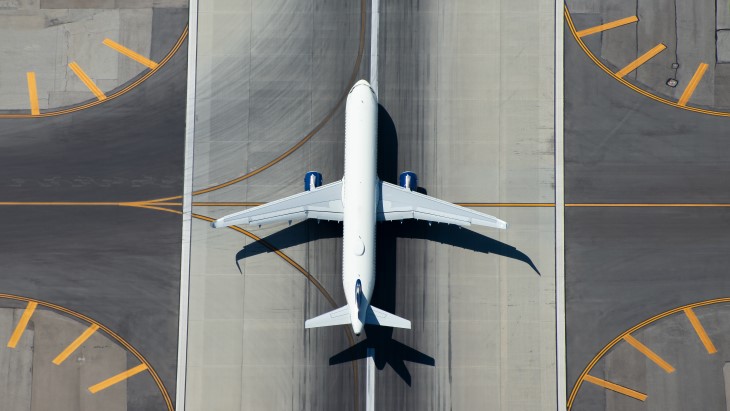
Herausforderungen und Innovationen der Materialien
Verbundwerkstoffe, eine Kombination verschiedener Materialien zur Schaffung eines Materials mit überlegenen Eigenschaften, haben die Fertigung in der Luftfahrtindustrie transformiert. Wie bereits erwähnt, sind sie die treibende Kraft hinter der Entwicklung von Flugzeugen, die nicht nur kraftstoffeffizienter, sondern auch stärker und langlebiger sind.
Glücklicherweise gibt es weiterhin Innovationen in der Herstellung von Verbundwerkstoffen, wie beispielsweise die Entwicklung von Hochleistungs-Harzen und Klebstoffen, kohlefasergestützten Materialien, Leichtbau, fortschrittlichen Polymerverbundwerkstoffen und mehr.
Hochleistungs-Harze und Klebstoffe
Hochleistungsanwendungen sind solche, bei denen Materialien, Produkte oder Technologien anspruchsvolle Leistungskriterien erfüllen müssen. Diese Anwendungen erfordern in der Regel eine überragende Leistung in Bezug auf Geschwindigkeit, Effizienz, Haltbarkeit, Präzision, Zuverlässigkeit oder eine Kombination dieser Faktoren. In der Luftfahrtindustrie müssen Hochleistungsprodukte in der Regel extremen Bedingungen standhalten, wie etwa hohen Temperaturen, Druck und Stress, und dabei Sicherheit und Effizienz gewährleisten.
Daher besteht für Materialien, die unter diesen Bedingungen arbeiten, ein großes Risiko für den Abbau ihrer Verbundschichten. Trotzdem haben jüngste Innovationen hochleistungsfähige Harze und Klebstoffe hervorgebracht, die diese Komplikationen durch eine stärkere Delamination zwischen den Schichten vermeiden.
Materialien auf Basis von Kohlefaser
Gängige Verbundwerkstoffe weisen möglicherweise nicht immer die vorteilhaftesten strukturellen Eigenschaften für Hochleistungsanwendungen in der Luftfahrt auf. Verbundwerkstoffe aus Kohlefaser hingegen zeichnen sich durch hervorragende Festigkeits-Gewichts-Verhältnisse, gute Schlagfestigkeit und insgesamt bessere Zähigkeit aus. Darüber hinaus besitzen Kohlefaserwerkstoffe außergewöhnliche Wärmeleiteigenschaften, die sie ideal für Flugzeug- und Luft- und Raumfahrtanwendungen machen.
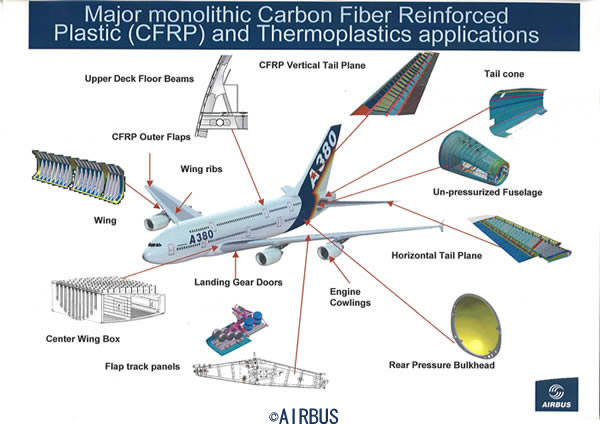
Gewichtsreduzierung
Um die Vorteile leichter Materialien in Flugzeugstrukturen weiter zu steigern, sind Materialinnovationen wie kohlefaserverstärkte Polymere (CFRP) und Schaumstoffkernverbundstoffe auf dem Vormarsch. Diese Materialfortschritte gewährleisten auch, dass die strukturelle Integrität und Leistung nicht beeinträchtigt werden.
Fortgeschrittene Polymerverbundstoffe
Um eine robuste Verbindung zwischen den Fasern und der Matrix in Verbundwerkstoffen sicherzustellen, wurden in jüngsten Innovationen verbesserte Bindungseigenschaften in Polymermatrizen eingeführt. Dadurch kann eine effektivere Verbindung zwischen einer Polymermatrix und Verstärkungsfasern hergestellt werden, was die Gesamtfestigkeit und Haltbarkeit des Materials erhöht.
Die Optimierung des Einsatzes von Kunststoffen und Verbundwerkstoffen in der Luftfahrtindustrie
Neben Innovationen in der Materialproduktion können technologische Lösungen wie sensXPERT Digital Mold die Herstellung von Kunststoff- und Verbundwerkstoffteilen optimieren. Im Falle von Digital Mold erfolgt dies durch die Charakterisierung des Verhaltens von Materialien in der Form während des Aushärtens mithilfe von dielektrischer Analyse, maschinellem Lernen und Materialmodellen.
sensXPERT sammelt wichtige Prozessdaten, darunter Fließfront, Vernetzungsgrad, Glasübergangstemperatur und Viskosität, um die Modelle zu trainieren und Echtzeitprognosen zum Materialverhalten während eines Aushärtungszyklus zu erstellen. Hersteller, die mit Digital Mold ausgestattet sind, erhalten somit tiefere Einblicke in die Materialeigenschaften, insbesondere in Bezug auf ihre Prozesse, was eine verbesserte Prozesskontrolle, gesteigerte Produktivität und insgesamt effiziente Produktion ermöglicht.
Wenn Sie mehr über unsere Lösung erfahren möchten, besuchen Sie unsere Seite Wie funktioniert senXPERT?
Erfahren Sie, wie ein führendes Luftfahrtunternehmen die Flugzeugproduktion revolutionierte!
Die Fertigung hochwertiger Flugzeugteile stellt höchste Ansprüche an Präzision, Effizienz und Qualität. In dieser spannenden Case Study erfahren Sie, wie ein führendes Luftfahrtunternehmen mit der sensXPERT-Technologie Prozesse digitalisierte, Zykluszeiten verkürzte, Materialabfall reduzierte und die Produktqualität auf ein neues Niveau hob. Lesen Sie, wie Echtzeitdaten, sensorgestützte Überwachung und KI-basierte Analysen entscheidend zur Transformation der Flugzeugproduktion beitrugen – und lassen Sie sich inspirieren, wie auch Sie von diesen Fortschritten profitieren können.
In diesem englischsprachigen Webinar erfahren Sie, wie ein führendes Luftfahrtunternehmen erfolgreich einen etablierten Fertigungsprozess mithilfe sensorgestützter und datenbasierter Technologie digitalisiert hat.