Wie Hersteller die Elastomerverarbeitung neu denken
Warum Echtzeitkontrolle das Rätselraten ersetzt – Teil für Teil.
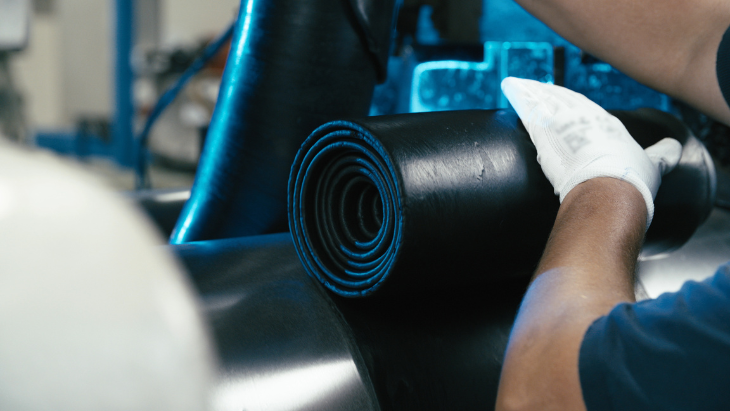
Kein Elastomer vulkanisiert wie das andere.
Elastomerbauteile können für das bloße Auge identisch erscheinen, sich aber unter Belastung, Temperatur oder im Laufe der Zeit völlig unterschiedlich verhalten. Genau das ist die Realität, mit der viele Hersteller in der Elastomerverarbeitung konfrontiert sind: das unvorhersehbare Verhalten einer Materialklasse, die zwar für ihre Flexibilität bekannt ist – aber nicht unbedingt für ihre Einheitlichkeit.
Da Produktspezifikationen immer anspruchsvoller werden und Toleranzen enger gefasst sind, erkennen Hersteller zunehmend, dass festgelegte Vulkanisationszeiten – meist basierend auf idealen Verarbeitungsbedingungen – selten mit der Realität in der Fertigungshalle übereinstimmen. Schwankungen in Chargen, Umgebungsbedingungen und Werkzeugverhalten können zu blinden Flecken führen, die die Bauteilqualität lange vor dem Start der Stoppuhr gefährden. Was steht wirklich auf dem Spiel? Die mechanische Integrität, die Langzeitbeständigkeit und die zuverlässige Leistung jedes Teils, das das Werkzeug verlässt.
Dieser Artikel beleuchtet die Komplexität der Elastomerverarbeitung und zeigt reale Produktionsherausforderungen sowie intelligentere Strategien zur Überwindung dieser Herausforderungen – weit über herkömmliche Qualitätskontrollen hinaus. Vom Verständnis, was jedes Elastomerbauteil einzigartig macht, bis hin zur Prognose der Bauteilperformance während der Vulkanisation – wir zeigen, wie Hersteller in ein neues Zeitalter der datengesteuerten Kontrolle eintreten.
Was sind Elastomere?
Elastomere sind eine Klasse von Polymeren, die für ihre hohe Elastizität bekannt sind. Ihre langkettige Molekularstruktur ermöglicht es ihnen, sich stark zu dehnen und dennoch in ihre Ursprungsform zurückzukehren. Diese Flexibilität – kombiniert mit der Widerstandsfähigkeit gegenüber schwankenden Temperaturen, Chemikalien, UV-Licht und Ozon – macht sie in zahlreichen Branchen unverzichtbar, von der Automobil- bis zur Luftfahrtindustrie.
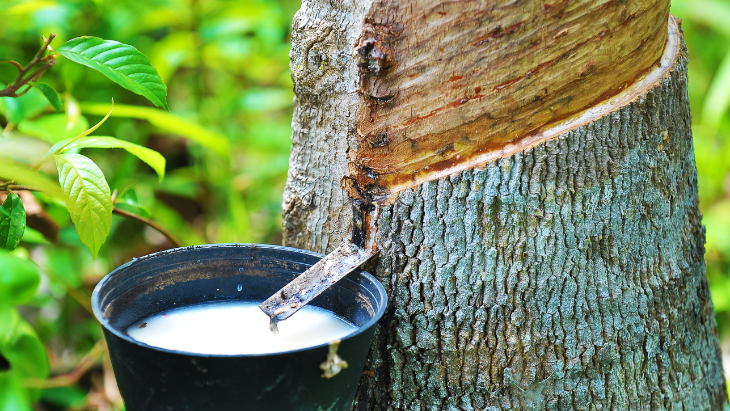
Elastomere lassen sich grob in drei Gruppen einteilen:
- Naturkautschuk: Aus Kautschukbäumen gewonnen und zu verwendbaren Mischungen verarbeitet.
- Synthesekautschuk: Aus fossilen Monomeren hergestellt, die Leistung wird durch Füllstoffe und Additive angepasst.
- Silikonkautschuk: Aus Quarzsand hergestellt, bekannt für exzellente Hitzebeständigkeit und Flexibilität.

Typische Anwendungen von Elastomeren:
- Dichtungen und O-Ringe
- Schläuche und Rohrleitungen
- Elektrische Isolatoren
- Schwingungsdämpfer
- Reifen und Schuhsohlen
Trotz der gemeinsamen Bezeichnung „Gummi“ unterscheiden sich Elastomere stark in Zusammensetzung und Verhalten.
Was macht ein Elastomer aus?
Elastizität: Können sich mehrfach ihrer Länge dehnen und kehren dennoch zu ihrer Ausgangsform zurück.
Resilienz: Stellen ihre Form nach Verformung wieder her.
Vernetzung: Vulkanisation bringt dauerhafte Bindungen ein, die das Material belastbar machen.
Vielfalt: Umfasst NBR, EPDM, Silikon, FKM und andere – jeweils mit unterschiedlichen Vulkanisationseigenschaften und Merkmalen.
Verständnis von Elastomertypen und Leistungsklassen
Der Begriff „Gummi“ wird oft synonym zu „Elastomer“ verwendet – doch es gibt einen entscheidenden Unterschied: Elastomer ist ein technischer Begriff für die gesamte Klasse elastischer Polymere. Gummi beschreibt meist eine Teilmenge davon – nämlich feststoffbasierte Mischungen wie Natur-, Synthese- oder Silikongummi.
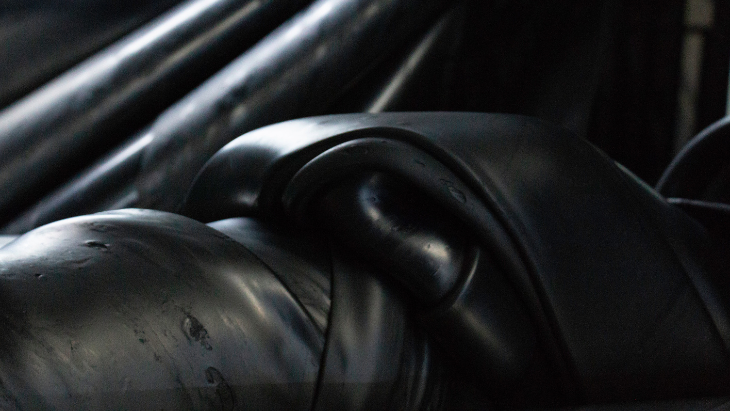
Selbst innerhalb eines einzelnen Elastomertyps – etwa EPDM – gibt es zahlreiche Formulierungen. Eine Variante vulkanisiert schnell bei 160 °C, während eine andere – abhängig von Füllstoffen oder Ölanteil – längere Zeiten benötigt. Häufig wird die genaue Rezeptur individuell auf die Anwendung abgestimmt – das Ergebnis ist eine enorme Vielfalt an Mischungen.
Und genau hier liegt ein zentrales Problem: Feste Zykluszeiten berücksichtigen keine materialbedingten Unterschiede.
Leistung vs. Preis bei Elastomeren
Standard-Elastomere (ca. 1–6 €/kg): NR, BR, SBR – z. B. in Reifen, Schuhsohlen, Latexprodukten.
Technische Elastomere (ca. 5–15 €/kg): EPDM, NBR, CR – z. B. in Dichtungen, Ventilen, Dämpfern.
Hochleistungs-Elastomere (ca. 15–400 €/kg): FKM, VMQ, FFKM – z. B. für extreme Medienbeständigkeit und hohe Lebensdauer.
–
Je höher Leistung und Preis, desto wichtiger ist ein präziser Prozess und eine gezielte Qualitätskontrolle.
Gängige Herstellungsverfahren für Elastomere
Die Umwandlung von Rohmischungen in funktionale Bauteile erfolgt über verschiedene Formungs- und Vulkanisationstechniken:
- Pressformen: Weit verbreitet, insbesondere für größere oder gestanzte Teile.
- Spritzgießen: Für hohe Stückzahlen und kurze Zykluszeiten.
- Spritzpressen: Gutes Maß an Kontrolle.
- Extrusion: Ideal für kontinuierliche Profile.
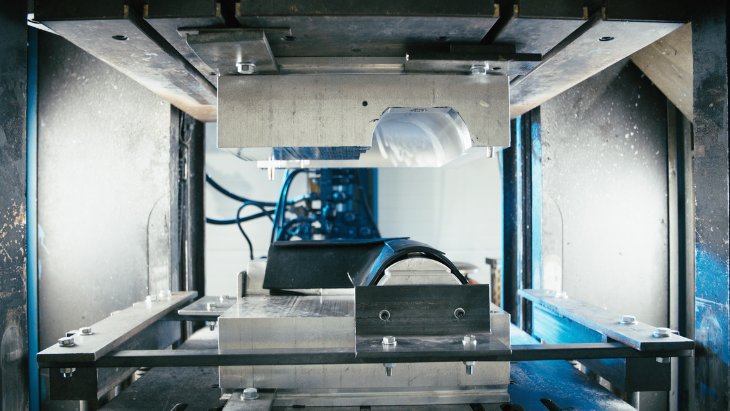
Jedes Verfahren bringt eigene Variablen mit sich. Doch die größte Unbekannte? Die Dynamik der Vulkanisation.
Die versteckten Risiken der Übervulkanisation
Viele Hersteller gehen auf Nummer sicher und verlängern Vulkanisationszeiten, um Untervulkanisation zu vermeiden. Doch diese Sicherheitsmarge kann sich rächen: Übervulkanisierte Bauteile zeigen schlechtere mechanische Eigenschaften, werden spröde, führen zu Ausschuss und verlängerten Zyklen – ohne garantiert bessere Qualität.
Noch problematischer: Diese Mängel bleiben oft unentdeckt, bis sie in der Endkontrolle auffallen – oder erst nach dem Versand.
Von übersehenen Defekten zu messbarer Performance
Solche Spätdefekte zeigen ein tieferes Problem auf. Herkömmliche Qualitätsmethoden – etwa Shore-Härte oder Zugfestigkeit – ignorieren oft das, was wirklich zählt: funktionale Vorhersagbarkeit.
- Besteht das Bauteil eine Spannungsprüfung?
- Haftet es korrekt am Leiter oder Gehäuse?
- Übersteht es thermische Zyklen langfristig?
Solche Fragen lassen sich nicht durch statische Tests beantworten. Hersteller brauchen Einblicke – in Echtzeit – direkt im Werkzeug.
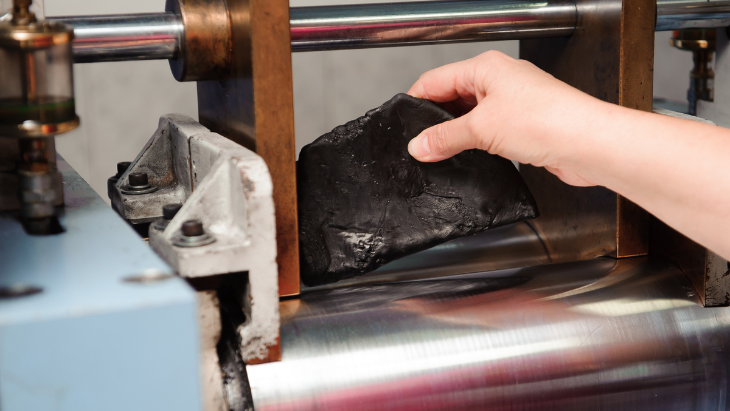
Die Herausforderung: Komplexe Materialien, verborgenes Verhalten
Trotz technischer Fortschritte bleibt ein Großteil der Elastomerproduktion weltweit stark manuell geprägt. Vom Mischen über Walzen bis zum manuellen Zuschneiden und Einlegen in Werkzeuge: Variabilität ist allgegenwärtig.
Auch externe Faktoren wie Raumtemperatur, Luftfeuchtigkeit oder die Zeitspanne, in der das Werkzeug geöffnet ist, beeinflussen das Ergebnis erheblich.
Hinzu kommt: Viele Werke arbeiten mit veralteten Maschinen und verlassen sich auf Erfahrungswerte statt digitale Systeme. Das Resultat? Eine Blackbox in der Mitte des Prozesses. Das Verhalten des Materials während der Vulkanisation bleibt unsichtbar.
Egal um welchen Typ es geht – eines ist klar: Kein Elastomer vulkanisiert wie das andere. Deshalb reichen Materialzertifikate oder Datenblätter allein nicht aus. Bereits kleinste Rezepturunterschiede führen zu deutlichen Abweichungen beim Aushärteverhalten und in der Bauteilleistung.
Warum in der Elastomerverarbeitung noch gerätselt wird
–
- Meist ist die Produktion stark manuell geprägt.
- Mischschwankungen, Bedienereinfluss und Umgebungsbedingungen führen zu Unvorhersehbarkeit.
- Viele Maschinen sind Jahrzehnte alt und nicht digitalisiert.
- Qualitätstests finden häufig erst nach der Produktion statt – zu spät für eine Korrektur.
–
Diese Herausforderungen erschweren eine stabile Elastomerverarbeitung.
Echtzeit-Prozesskontrolle: Intelligenter Vulkanisieren
Hier kommt sensXPERT ins Spiel.
Unsere Lösung bringt Echtzeittransparenz in die Elastomerverarbeitung. Mithilfe dielektrischer Sensortechnologie im Werkzeug überwachen wir die molekulare Reaktion des Materials – etwa durch Messung der Ionenbeweglichkeit – und bestimmen den Vulkanisationsgrad, die Kinetik und das Materialverhalten.
Wir visualisieren den Fortschritt, erkennen Abweichungen und prognostizieren die Ergebnisse – während das Bauteil noch entsteht.
So können Hersteller den Zyklus exakt dann beenden, wenn das Material optimale Eigenschaften erreicht hat. Das Resultat? Bessere Bauteile, weniger Ausschuss, kürzere Zykluszeiten.
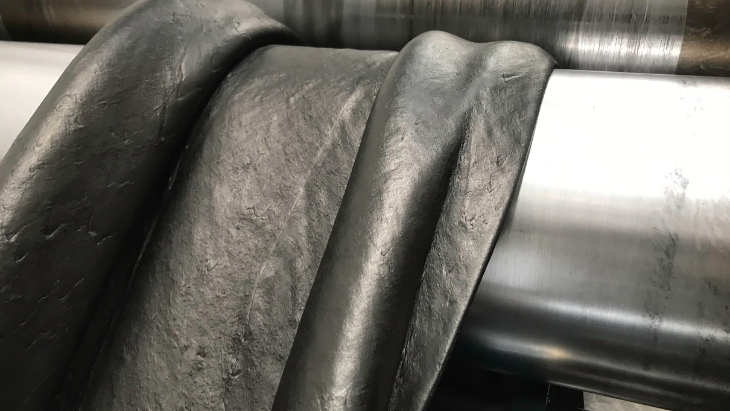
Bewährte Ergebnisse: 15 % schneller, 100 % intelligenter
Unsere Zusammenarbeit mit NETZSCH Pumps & Systems belegt den praktischen Mehrwert smarter Elastomerverarbeitung. Durch den Einsatz von sensXPERT Insight in der Gummistatorfertigung konnten sie:
- Die Zykluszeit um 15 % senken
- Vollständige Transparenz im Werkzeug erreichen
- Die Produktionseffizienz steigern
Lesen Sie die vollständige Fallstudie und sehen Sie die Ergebnisse selbst.
Willkommen in der Zukunft der Elastomerverarbeitung
Der Modernisierungsbedarf war noch nie so dringlich. Steigende Lohnkosten und zunehmender globaler Wettbewerb setzen Hersteller unter Druck – insbesondere, wenn die Produktion noch stark manuell abläuft. Selbst Regionen mit traditionell niedrigen Produktionskosten sehen sich nun Margendruck ausgesetzt.
In diesem kostenkritischen Umfeld sind Ausschussvermeidung, kürzere Zykluszeiten und fehlerfreie Endprodukte entscheidend für Wettbewerbsfähigkeit und Profitabilität.
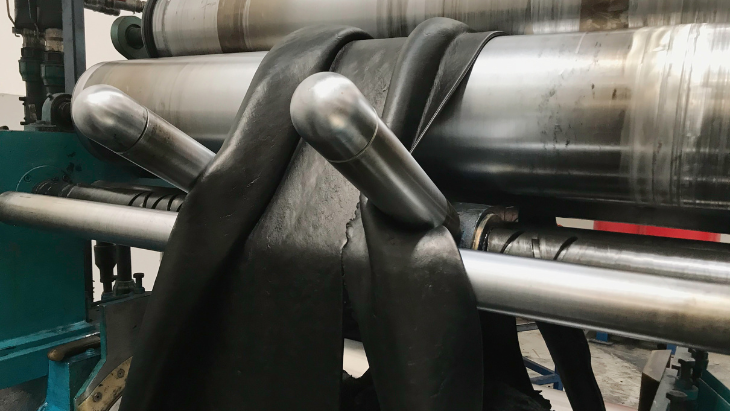
Wir stehen erst am Anfang. Egal ob NBR, EPDM, Silikon oder andere Materialien – sensXPERT passt sich Ihren Prozessen und Materialrealitäten an.
Verlassen Sie sich noch auf feste Zykluszeiten und statische Tests? Lassen Sie uns das gemeinsam ändern.
Abonnieren Sie unseren Newsletter und verpassen Sie nicht unser kommendes Webinar zur Elastomerverarbeitung.
Die Zukunft der Elastomerverarbeitung ist nicht reaktiv – sie ist vorausschauend. Denken wir sie neu. Teil für Teil.